Ceramica
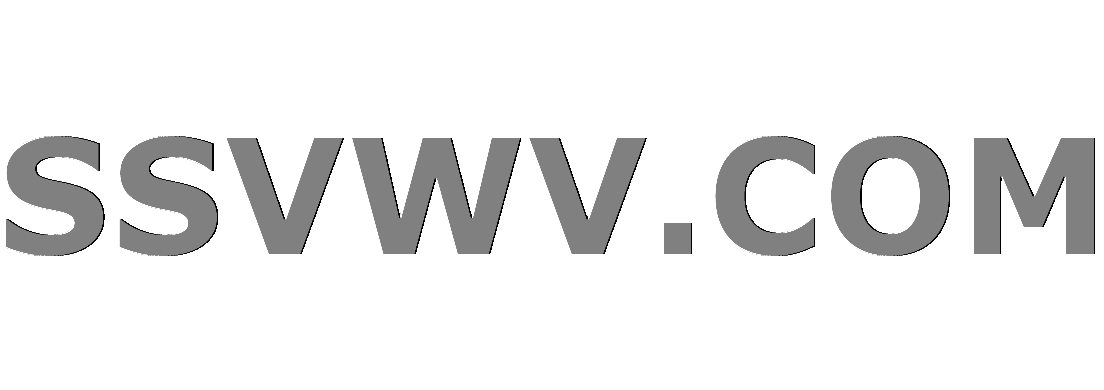
Multi tool use
.mw-parser-output .nota-disambigua{clear:both;margin-bottom:.5em;border:1px solid #CCC;padding-left:4px}.mw-parser-output .nota-disambigua i{vertical-align:middle}
Questa voce o sezione sugli argomenti materiali e arte non cita le fonti necessarie o quelle presenti sono insufficienti. |

Cina, cultura di Yangshao, giara del Neolitico (2000 a.C. circa), Walters Art Museum

Messico occidentale, Nayarit meridionale, figura di guerriero con bastone (III secolo a.C.-IV secolo d.C.), Museo internazionale delle ceramiche in Faenza

Grecia, Attica, Pittore di Trittolemo, kylix a figure rosse con il Festino di Apaturia (480 a.C. circa), Louvre

Afghanistan, Herat, Moschea del Venerdì decorata da piastrelle maiolicate (XII secolo)

Andrea della Robbia, Madonna della Cintola (1500 circa), Liebieghaus

Germania, Meissen, Johann Joachim Kaendler, statuetta in porcellana con Signora con tavolino e servitore moro (1740 circa), Kunstgewerbemuseum
La ceramica (dal greco antico κέραμος, 'kéramos', che significa "argilla", "terra da vasaio") è un materiale inorganico, non metallico, molto duttile allo stato naturale, rigido dopo la fase di cottura.
Con la ceramica si producono diversi oggetti, quali stoviglie, oggetti decorativi, materiali edili (mattoni, piastrelle e tegole), rivestimenti per muri e pavimenti di abitazioni. Specifiche ceramiche inoltre, trovano impiego nei rivestimenti ad alta resistenza al calore per il loro alto punto di fusione. Il colore del materiale ceramico varia a seconda degli ossidi cromofori contenuti nelle argille (ossidi di ferro, da giallo, arancio, rosso a bruno; ossidi di titanio, da bianco a giallo). Può venire smaltata e decorata.
La ceramica è usualmente composta da diversi materiali: argille, feldspati, (di sodio, di potassio o entrambi), sabbia silicea, ossidi di ferro, allumina e quarzo. Una composizione così articolata determina la presenza di strutture molecolari appiattite dette fillosilicati. La forma di questi, in presenza di acqua, conferisce all'argilla una certa plasticità e ne rende la lavorazione più facile e proficua. Un manufatto in terracotta o argilla è detto fittile.
Indice
1 Tipi di ceramiche
1.1 Le terrecotte
1.2 Il grès
1.3 La porcellana
1.4 L'argilla
2 Prodotti in ceramica
3 Cenni storici
4 Il ciclo produttivo
4.1 Selezione e preparazione dell'argilla
4.2 Lavorazione dell'argilla
4.3 Modellazione
4.3.1 Modellazione a mano libera
4.3.2 Modellazione a colombino
4.3.3 Modellazione a lastre
4.3.4 Modellazione al tornio
4.3.5 Modellazione a stampo
4.4 Essiccazione
4.5 Cottura
4.6 Smaltatura e decorazione
4.7 Produzione industriale di piastrelle ceramiche
4.7.1 Preparazione delle materie prime, essiccazione, cottura
4.7.2 Smaltatura e ricottura
5 Produzione di ceramica in Italia
6 Produzione di ceramica in Giappone
7 Note
8 Bibliografia
9 Voci correlate
10 Altri progetti
11 Collegamenti esterni
Tipi di ceramiche |
La ceramica è una lavorazione antica e molto diffusa in aree anche molto distanti tra loro. Esistono tipi diversi di ceramiche:
ceramiche a pasta compatta. Rientrano nel gruppo i gres e le porcellane. Hanno una bassissima porosità e buone doti di impermeabilità ai gas e ai liquidi. Non si lasciano scalfire neanche da una punta d'acciaio.
ceramiche a pasta porosa. Sono tipicamente le terraglie, le maioliche e le terrecotte. Hanno pasta tenera e assorbente, più facilmente scalfibile.
Le tipologie ceramiche principali sono: la terracotta o coccio, la terraglia, la maiolica, il gres e la porcellana che può essere a pasta tenera o dura.
Le terrecotte |
.mw-parser-output .vedi-anche{border:1px solid #CCC;font-size:95%;margin-bottom:.5em}.mw-parser-output .vedi-anche td:first-child{padding:0 .5em}.mw-parser-output .vedi-anche td:last-child{width:100%}
Sono ceramiche che, dopo il processo di cottura, presentano una colorazione che varia dal giallo al rosso mattone, grazie alla presenza di sali o ossidi di ferro[1]. La cottura si effettua a 980- 990 °C. La presenza di ossido di ferro, oltre a dare il colore tipico, migliora anche la resistenza meccanica della ceramica cotta, contribuendo alla vetrificazione e quindi riducendo la porosità del manufatto.
Grazie alla sua stabilità, alla resistenza all'invecchiamento, e alla leggerezza che deve alla sua porosità, la terracotta è il più diffuso materiale da costruzione, chiamato con il nome di laterizio[2]. La terracotta si distingue generalmente dal laterizio per una "più accurata depurazione delle argille"[1].
Sono utilizzate sia senza rivestimento superficiale che con rivestimento. Le prime come ceramica strutturale e ornamentale: laterizi, vasi, brocche, ecc. Le seconde anche come vasellame da cucina: tazze, piatti.
Il grès |
Il grès è utilizzato soprattutto per produrre mattonelle per i bagni e le cucine. Si ottiene per mescolanze argillose naturali che producono ceramiche dette, appunto, greificate. È necessaria una temperatura tra 1200 °C e 1350 °C. I colori variano a seconda dei composti ferrosi presenti. Per ottenere grès bianchi si utilizzano impasti artificiali a base di argille cuocenti bianche e rocce quarzoso-feldspatiche che inducono la greificazione della massa. Possono venire smaltate: come per tutte le altre ceramiche, dopo la cottura vengono colorate allo stesso livello dell'impasto, che contiene, di solito, un 33% circa di argille caolinitiche (bianche), un 50% di fondenti (principalmente feldspato) e la percentuale restante di materiali inerti (sabbie o quarzo).
La porcellana |

Composizione floreale (porcellana di Capodimonte)
È considerata il più "alto" livello di produzione ceramica per gli orientali. Principale componente ne è una particolare argilla bianca: il caolino idrosilicato di alluminio - Al2O3·2 SiO2·2 H2O. È stata inventata in Cina attorno all'VIII secolo ed è realizzata appunto con caolino, silice (o sabbia quarzosa) e feldspato.
Il caolino conferisce, ma non sempre, le proprietà plastiche e il colore bianco della porcellana; il quarzo è il componente inerte e svolge la funzione di sgrassante (inoltre consente la vetrificazione); infine il feldspato che viene definito fondente, perché, fondendo a temperature più basse del caolino, abbassa notevolmente la cottura dell'impasto ceramico (1280 °C). Esistono tipi anche molto diversi di porcellana, tipici delle diverse tradizioni di produzione.
L'argilla |
La temperatura di cottura dell'argilla è in funzione del tenore di Allumina in essa contenuta. L'argilla è naturalmente molto malleabile, in quanto la presenza di acqua nella sua struttura ne migliora le caratteristiche plastiche ed è quindi molto facile da lavorare anche con le mani. Quando è asciutta, ma non ha ancora subìto il processo di cottura, diventa rigida e fragile. Se sottoposta ad un intenso riscaldamento, diventa permanentemente solida.
Prodotti in ceramica |
Con la ceramica non si intende solo il materiale, ma per estensione anche il prodotto che di quel materiale risulta composto.
I prodotti in questione possono essere moltissimi. Tra i più frequenti merita ricordare:
ceramici tradizionali. Sono utilizzati nell'industria edilizia;
da rivestimento e da copertura. Sono le tegole e le piastrelle;
strutturale. Sono i laterizi;
sanitari;
meccanici e aeronautici, soprattutto nei motori e turbine.
Le piastrelle, inoltre, possono venire suddivise in:
non smaltate: cotto, grès rosso, clinker e, in alcuni casi, gres porcellanato;
monocottura: può essere rossa, bianca e clinker.
Questi due tipi danno luogo a ceramiche tecniche, con assorbimento di acqua da scarso a nullo:
- in bicottura: prevalentemente la maiolica;
- in cotto forte e terraglia. Entrambe caratterizzate da un forte assorbimento di acqua.
Esistono anche padelle con rivestimento interno in ceramica (smalti bassofondenti per lamiera), che laddove applicato con tecnologie appropriate conferisce caratteristiche di antiaderenza e non presenta il rischio del Teflon di rilasciare tetrafluoroetilene ad alte temperature.
Cenni storici |
La ceramica è conosciuta fin dai periodi preistorici e si suppone che la sua invenzione sia avvenuta solo due volte nella storia dell'umanità: tra le popolazioni sahariane e in Giappone[3]. Da questi luoghi d'origine si è poi diffusa in tutto il mondo.
I resti di ceramica più antichi al mondo si trovano nei siti della grotta di Yuchanyan (Hunan, Cina), dove sono datati col metodo del carbonio-14 16100-14500 a.e.v. e a Miaoyan (Guangxi, sempre in Cina), qua invece datati 17100-15400 a.e.v.[4] L'antichità di tali siti è pari, se non superiore d'alcuni millenni,[5] ai siti corrispondenti in Giappone del principio del periodo Jōmon, i siti di Simomouchi e di Odai Yamamoto datati 17000 e 15000 a.e.v.[6]
Successivamente l'arte vide l'introduzione del tornio, che consentì di ottenere facilmente oggetti aggraziati e di perfetta simmetria rispetto all'asse di rotazione. La ceramica dipinta venne esportata dall'Anatolia e dai territori siriaci verso l'Europa intorno al III millennio a.C., dove però prevalse l'interesse per le forme e per le anse.
L'introduzione della verniciatura vetrosa, in uso a partire dal II millennio a.C. in Mesopotamia, migliorò ulteriormente la resistenza all'usura e le caratteristiche estetiche. Una vera rivoluzione si ebbe con la scoperta della lavorazione della porcellana, che si fa risalire all'VIII secolo d.C. in Cina.
Altri centri antichi di notevole importanza risultarono quelli iraniani, come ad esempio Tepe e indiani, come Daro e Harappa.

Wedgwood, copia del Vaso Portland in gres (1790 circa), Cleveland Museum of Art
L'antica Grecia ereditò la tecnica della ceramica dalla civiltà minoico-micenea. Dal VI al V secolo a.C. Atene dominò i mercati con la sua produzione di vasi, ma nel IV secolo a.C. questa decadde. Sorsero altre fabbriche locali in Beozia, Etruria, Magna Grecia e Sicilia. La produzione di queste lasciò un segno tanto profondo che, molti secoli, dopo, Josiah Wedgwood chiamò Etruria la sua manifattura di porcellane, destinata a diventare una delle più famose del mondo.
In età augustea si diffuse la ceramica aretina, con decorazione a rilievo. A questa seguì in tutto l'Occidente romano la ceramica a rilievo detta "terra sigillata", che rimase in uso fino al termine dell'impero.
Intorno all'anno mille sorse in Europa, nel tentativo di imitare i prodotti orientali, la maiolica.
Nel tardo Medioevo le ceramiche venivano realizzate con il tornio, cotte al forno e impermeabilizzate con una vernice vetrosa. Dopo il XIII secolo si incominciano ad usare anche altri colori e decorazioni più sofisticate. In questo periodo l'Italia peninsulare sviluppò i maggiori centri di produzione: Forlì, poi superata dalla vicina Faenza, Pisa, Siena e Orvieto, mentre più a sud si affermò Ariano;[7] la produzione siciliana si concentrò invece a Caltagirone. Nel XV secolo si elaborarono varie forme decorative, sia per la coloristica sia per le cosiddette storie o racconti descritti e raffigurati. La produzione di questo periodo è ben rappresentata, ad esempio, dal celebre servizio realizzato da Nicola d'Urbino per Isabella d'Este e per la corte dei Gonzaga.[8] Il secolo XVII fu al centro di una grande importazione di prodotti cinesi che influenzò il gusto europeo. Solamente agli inizi del Settecento l'alchimista tedesco Böttger a Meissen riuscì a produrre una ceramica dura, almeno quanto quella cinese, la porcellana, grazie alla scoperta del caolino.[9]
Verso la fine dell'Ottocento la produzione di ceramica prende corpo, grazie all'introduzione di alcune tecniche industrializzate. In Italia, nel modenese, si mette a punto una tecnica che permette di aumentare la produzione di piastrelle, all'epoca in uso quasi solo in cucina e bagno.
Negli anni cinquanta del Novecento si introducono altre consistenti migliorie, quali la pressa automatica e il forno a tunnel. Con queste varianti alla produzione si riesce infine a raggiungere una produzione su scala medio-larga, necessaria per sostenere un mercato in forte espansione. Ma è negli anni sessanta e settanta che il mercato della ceramica in Italia vede una vera impennata. La produzione viene completamente automatizzata in tutte le sue fasi e viene introdotto un nuovo macchinario: l'atomizzatore.
Questo consentì di sostituire i filtri pressa usati nella preparazione ad umido degli impasti. Dagli anni ottanta in poi, infine, ci si è concentrati soprattutto sulle tecniche di cottura veloce (cottura rapida monostrato) e sulla riduzione dell'impatto ambientale della produzione. Da pochi anni vengono utilizzati anche per la costruzione di dischi per impianti frenanti, mescole di carbonio e ceramica, in grado di diminuire l'effetto del fading; e poi anche per il suo peso contenuto; ancora in fase di progetto viene montato solo su vetture di alto livello, come Ferrari, Porsche e Lamborghini.
Da sottolineare oggi la valenza che la modellazione ceramica ha assunto in campo educativo sia per lo sviluppo delle attività manuali e creative sia nel settore del recupero cognitivo.[10]
Il ciclo produttivo |

Giappone, periodo Jōmon (5.000 a.C. circa), Birmingham Museum of Art (Alabama)
Il ciclo produttivo prevede vari passaggi, a seconda del risultato che si desidera ottenere e a seconda che la produzione sia artigianale o industriale.
Selezione e preparazione dell'argilla |
L'argilla viene anzitutto selezionata per la lavorazione che si intende portare avanti. I tre tipi di argilla usata sono:
Caolino. Presenta bassa plasticità, colore bianco, scarso potere essiccante ed è refrattario. È usato nelle porcellane cinesi.- Argilla sabbiosa. Presenta alta plasticità e grana fine.
- Argille refrattarie. Sono specialmente resistenti al fuoco.
Quale che sia l'argilla che si utilizzerà, essa non è direttamente utilizzabile per il processo se si trova ancora al suo stato naturale. Deve venire ripulita dalle impurità e per ottenere questo si procede alla fase della stagionatura. Successivamente viene sciolta in acqua per la lavatura, che causa la dispersione dei sali solubili. Infine subisce un'ulteriore depurazione per eliminare le residue impurità e soprattutto per affinarla, togliendo le particelle a granulometria più grossolana.
Lavorazione dell'argilla |
Selezionata e ripulita, si procede a impastare l'argilla. Questa fase tende a eliminare eventuali bolle d'aria e a renderla compatta, per prevenire il formarsi di crepe nel prodotto finito. All'impasto si aggiunge, talvolta, della "chamotte", ovvero polvere ottenuta dalla macinazione della ceramica precedentemente cotta, con lo scopo soprattutto di rendere il prodotto resistente agli sbalzi repentini di calore. L'aggiunta della chamotte è, ad esempio, quasi indispensabile nel Raku Giapponese e nel Raku Americano a Fumo.
Modellazione |
Un'arte tanto antica ha accumulato nei secoli varie tecniche di modellazione. Tra di esse ricordiamo:
- modellazione a mano libera;
- modellazione a colombino;
- a lastre;
- al tornio;
- allo stampo.
Modellazione a mano libera |
È la più antica ed è simile a quanto fanno i bambini quando giocano con la plastilina: si prende una porzione di argilla e, con il solo uso delle mani, si modella la forma desiderata. È possibile avvalersi dell'ausilio di alcuni strumenti, come le stecche o gli occhielli per le rifiniture dell'oggetto modellato.
Modellazione a colombino |
Questo tipo di modellazione, chiamata anche a lucignolo, prevede l'uso e l'assemblaggio dei colombini di argilla. Si dividono blocchi di argilla delle dimensioni di un sigaro e si stendono con i palmi delle mani, ottenendo dei lunghi cilindri simili a lunghi grissini. Si arrotolano questi colombini gli uni sopra gli altri, si uniscono fra di loro e si lisciano per ottenere una superficie compatta. Con questa lavorazione, ugualmente antica, si modellano soprattutto vasi e ciotole.
Modellazione a lastre |
Si prende un pane d'argilla e se ne tagliano lastre di spessore omogeneo usando un filo o stendendole con un matterello. Successivamente le lastre vengono tagliate a stampo oppure giuntate tra loro con l'aiuto di incisioni spalmate con barbottina.
Modellazione al tornio |

Corea, lavorazione di argilla al tornio tradizionale
È usato soprattutto per la produzione di vasellame in cui vi sia una simmetria rispetto all'asse di rotazione. Il tornio è formato da un supporto girevole, simile ad un piatto la cui velocità viene stabilita tramite un pedale, come nel tornio antico, o tramite motorino regolato da reostato, ai giorni nostri.
Si pone una data massa di argilla al centro del piatto girevole, avendo cura di posizionarla perfettamente in centro. Quindi si modella con uso delle mani o di altri strumenti mentre si regola la rotazione del tornio stesso. La massa di argilla che si è deciso di usare all'inizio deve essere sufficiente a formare tutto l'oggetto, dal momento che non è possibile aggiungerne in corso d'opera senza pregiudicare la forma data con la modellazione. Questo non è vero in termini assoluti, per vasi di grandi dimensioni, con altezze e diametri superiori agli 80 cm è comune nei tornianti professionisti la pratica di aggiungere colombini di terra all'oggetto in formatura e proseguire nella lavorazione per raggiungere dimensioni notevoli.
Modellazione a stampo |
In questa modellazione si prepara, anzitutto, uno stampo in gesso, che replica l'oggetto che si intende riprodurre. Quindi vi si cola dentro argilla liquida chiamata anche colaggio e dopo un tempo adeguato in cui il gesso fornisce all'oggetto sufficiente spessore, assorbendo l'acqua del colo, il colaggio superfluo viene versato e si attende pazientemente che l'oggetto asciughi. Viene quindi estratta dallo stampo e rifinita a mano. Dopo un tempo utile all'asciugatura, il pezzo verrà poi messo in forno per la 1ª cottura (biscotto).
Vi sono altri tipi di formatura con stampo in gesso a calco, si forma una lastra di argilla di circa 10/15 mm di spessore a seconda della grandezza del pezzo, si procede fornendo una pressione omogenea all'impasto argilloso per non variare gli spessori dell'oggetto da riprodurre sino a coprire tutta la superficie dello stampo.
Un altro procedimento è chiamato a pressatura (o procedimento RAM). Viene usata argilla più dura e vengono usate due matrici di stampo, una maschio e una femmina, e una che si incastra sull'altra lasciando all'interno il vuoto che viene occupato dall'argilla. Gli stampi si montano su una macchina che si chiama pressa, ponendoli uno di fronte all'altro, con una dose di argilla sufficiente per foggiare l'oggetto quando la macchina inizia il suo ciclo. Le due superfici si avvicinano e foggiano l'argilla all'interno dello stampo.
Essiccazione |
Qualunque sia la tecnica che si è adottata, è necessario che i manufatti in argilla essicchino completamente all'aria. A questa fase va dedicata una particolare cura. Una essiccazione omogenea e uniforme è garanzia di durevolezza dell'oggetto finito e soprattutto della coerenza della sua forma: un'essiccazione non uniforme può generare deformazioni. Solo dopo questa fase si può procedere alla cottura. L'essiccazione, infatti, consente all'oggetto di perdere l'umidità residua e la sua plasticità. Viene così fissata la forma che si è inteso dargli.
Dopo un certo periodo di essiccazione l'argilla raggiunge lo stadio adatto ad essere incisa e decorata. Tale stadio è detto della stadio della durezza cuoio: l'argilla è infatti già indurita, ma mantiene ancora una certa residua plasticità.
Cottura |

Vasi di terracotta
Terminata la delicata fase dell'essiccazione si procede con quella della cottura. Questa avviene in forni appositi, che raggiungono temperature che possono andare parecchio oltre i 1000 °C fino i 1500 °C. Il processo può durare anche molte ore. È infatti necessario che la temperatura segua curve di crescita e decrescita graduali e prestabilite, e che tutte le varie fasi abbiano una durata prestabilita. In seguito alla cottura il prodotto subisce un'ulteriore riduzione di volume.
Poiché la cottura modifica la struttura del prodotto finale, modulandola si possono ottenere risultati diversi:
Terracotta - si ottiene mantenendosi tra 960 e 1030 °C
Terraglia tenera - si ha tra 960 e 1070 °C
Terraglia dura - si ha tra 1050 e 1150 °C
Gres - si ottiene tra 1200 e 1300 °C. Il Gres è un prodotto fortemente vetrificato, impermeabile e poco poroso. Prodotti quali il klinker, il ball clay, e il fireclay appartengono a questa famiglia
Porcellana tenera - si ha tra 1200 e 1300 °C, previo utilizzo di caolino. A questo stadio otteniamo sia la vetrificazione, sia la traslucidità, sia l'impermeabilità.
Porcellana dura - si ha tra 1300 e 1400 °C. È di solito di uso industriale.
Ceramica High-Tech - si ottiene tra 1400 e 1700 °C, previo utilizzo di sostanze aggiuntive, quali caolino e allumina.
Nelle diverse fasi della cottura, inoltre, avvengono varie trasformazioni:
- tra la T ambiente e 200 °C - si elimina l'acqua igroscopica residua nell'impasto e quella contenuta da alcuni sali, come ad esempio il gesso
- tra i 250 °C e i 350 °C - le materie organiche vanno in combustione. Viene liberata l'acqua zeolitica chimicamente combinata
- tra i 450 °C e i 850 °C - si decompongono i minerali delle argille, liberando l'acqua reticolare
- 850 °C - si decompongono i carbonati (decarbonatazione) e si ossidano i solfuri
- tra i 1100 e 1200 °C - fondono i feldspati, e si ottiene la vetrificazione
Va ricordato, infine, che la presenza di ossigeno in camera di combustione determina il degrado delle sostanze organiche presenti, nonché l'ossidazione delle sostanze minerali. Come risultato si ottiene un prodotto di color rosso ruggine per azione dell'ossigeno (ossidante) sul ferro. Si otterrà, invece, un colore nero scuro per azione del vapore e monossido di carbonio (riducente).
Smaltatura e decorazione |
Spagna, grande piatto a lustro, (XVI secolo), Musée des Arts Décoratifs (Parigi)
Ci sono molti modi di decorare e colorare la ceramica, anche in relazione al tipo di risultato che si desidera ottenere e alla cottura cui si sottoporrà il pezzo. I colori da ceramica sono essenzialmente di tre tipi:
Ingobbio - sono specifici colori per la decorazione della ceramica composti da argille già cotte e finissimamente triturate, caolino, sostanze minerali e ossidi. Sono, di fatto, smalti adatti a poter venire applicati sull'oggetto essiccato, ma ancora crudo e da cuocere. Questo permette di saltare un passaggio e cuocere l'oggetto una sola volta, dal momento che questi colori particolari tollerano l'alta temperatura cui si sottopone la ceramica. Gli ingobbi non sono tanto largamente diffusi, essendo costosi e dalle tinte tenui. Perché raggiungano la vetrificazione, inoltre, è necessario portare l'oggetto alla medesima temperatura dell'argilla che si ritrova nella composizione dell'ingobbio. Molti ceramisti che apprezzano la tecnica preparano da sé gli ingobbi che desiderano usare.
Cristalline, dette anche Vetrine. Sono rivestimenti di tipo vetroso, impermeabili e lucidi. Usualmente trasparenti, solo occasionalmente sono colorate. Lasciano intravedere l'argilla sottostante. Alle cristalline si aggiungono fondenti, quali il germanio (che sostituisce il tossico ossido di piombo), gli alcali o i borati. Questo allo scopo di abbassare il punto di fusione.
Smalti - anch'essi di tipo vetroso. A differenza delle cristalline non sono trasparenti, ma coprenti. Ciò è determinato dalla presenza di componenti quali il feldspato potassico o sodico, stagno ossido, titanio ossido, alluminio ossido (allumina), zirconio ossido o silicato e altri ancora. Possono avere aspetto lucido o satinato: nel secondo caso la presenza di ossido di calcio e/o zinco nello smalto, provvedono, in fase di raffreddamento, ad una cristallizzazione sulla superficie dello smalto devetrificandolo, ossia togliendo brillantezza.
La smaltatura di un pezzo in ceramica ha lo scopo di proteggere il pezzo dall'usura, di facilitarne la pulitura e la manutenzione e di decorarlo.
Se il pezzo viene smaltato e non colorato all'ingobbio la smaltatura avviene dopo la cottura e si utilizzano appositi smalti composti da una miscela in vari rapporti di vetro, opacizzanti, fondenti e terre. La smaltatura classica, pertanto è detta applicata al biscotto, ovvero all'oggetto già passato in cottura.
Anche per la smaltatura vi sono svariate tecniche, tra le quali ricordiamo:
- smaltatura ad aerografo
- smaltatura per immersione
- pittura a smalto
- smaltatura a campana
- smaltatura elettrostatica
Dopo che si sia provveduto a smaltare la superficie dell'oggetto, si passa alla decorazione pittorica che è usualmente fatta a mano con pennello e colori ceramici. Questi colori ceramici sono ottenuti da ossidi minerali oppure da ossidi metallici addizionati di fondenti o indurenti. Dopo la smaltatura e la decorazione si procede con una seconda cottura, il cui scopo è quello di fissare lo smalto all'oggetto.
Come si è detto, gli oggetti sottoposti a smaltatura classica devono subire una seconda cottura per fissare i colori. Tale cottura si attua in forno ad una temperatura compresa tra i 850 e i 970 °C, a seconda dei fondenti utilizzati nello smalto e sempre al di sotto della temperatura utilizzata per la prima cottura.
Questa seconda cottura porterà lo smalto a vetrificare, rendendolo lucido e impermeabile. Poiché l'umidità dello smalto è scarsa e i pericoli di rottura sono conseguentemente bassi, la curva della temperatura può essere innalzata più velocemente.
Produzione industriale di piastrelle ceramiche |
I processi fondamentali sono due:
- monocottura - la materia prima viene generalmente approntata con processo a processo ad umido e l'essiccazione è a spruzzo. Vi è una sola fase di cottura, dopo che il pezzo è stato essiccato e smaltato. Durante questa cottura singola avvengono anche i processi di sinterizzazione e stabilizzazione dello smalto.
- bicottura - in questo caso la preparazione della materia prima segue quasi sempre un processo a secco. Vi sono due fasi di cottura. Nella prima avviene la sinterizzazione del supporto. Segue la cottura dello smalto.
Il ciclo produttivo industriale è composto da varie fasi. Tra queste ricordiamo: preparazione delle materie prime, formatura, essiccamento, smaltatura, cottura e scelta. I due terzi della produzione industriale italiana attuale sono occupati dal Grés porcellanato, di cui la metà viene smaltata.
Preparazione delle materie prime, essiccazione, cottura |
Lo scopo della preparazione delle materie prime è ottenere un impasto di composizione omogenea, con una distribuzione granulometrica e forma dei grani appropriata. La granulometria fine permette una giusta velocità di essiccamento e una corretta reattività in fase di cottura. La forma dei grani e l'umidità dell'impasto influenzano l'uniformità del pressato.
Infine l'impasto deve presentare un contenuto d'acqua adatto al sistema di formatura che si è scelto. I sistemi di formatura sono:
- pressatura - interessa soprattutto il settore delle piastrelle e comporta un 5-6% di acqua.
estrusione - è in uso soprattutto per i laterizi e comporta un 20 % di acqua- colaggio - è il sistema adottato per i sanitari e presenta un contenuto di acqua del 40%
Dopo la formatura ha luogo il processo di essiccazione e successivamente quello di cottura. I materiali ceramici possono essere ottenuti da polveri tramite un processo detto di sinterizzazione. Questo processo chimico-meccanico avviene in forni ad altissime temperature dove le polveri si fondono dando origine ai materiali ceramici. In particolare il feldspato, portato ad alte temperature, forma un eutettico, assieme al quarzo della sabbia e ai prodotti di decomposizione dell'argilla, che fondendo avvolge le rimaneti parti.
Dopo l'essiccazione normalmente i prodotti modellati subiscono il processo di cottura, che conferisce maggiore resistenza meccanica ai manufatti ed elimina l'acqua residua rimasta dopo l'essiccamento.
Smaltatura e ricottura |
La smaltatura può avvenire tra la prima cottura e la seconda o prima della cottura unica. Lo scopo, è duplice: da un lato estetico, dall'altro pratico. Che lo smalto sia vetrina trasparente o smalto colorato il risultato finale è l'impermeabilizzazione e l'isolamento termico. Nelle ceramiche si aggiungono ossidi di piombo agli smalti, per abbassarne il punto di cottura e risparmiare sui costi. Le porcellane, usano la vetrina senza piombo e la ricottura a 1500 °C.
Produzione di ceramica in Italia |
L'Italia è leader nel commercio internazionale della ceramica con una quota del 35% in termini di volumi e di valori.[11]
Talune manifatture di antica origine si fregiano del marchio CAT (Ceramica Artistica Tradizionale) rilasciato dal Consiglio Nazionale Ceramico[12]:
ceramica di Albissola (Liguria), secoli XVI-XVIII;
ceramica di Ariano Irpino (Campania), attestata fin dal XIII secolo;
ceramica di Caltagirone (Sicilia), secoli XVI-XVIII;
ceramica di Cerreto Sannita e di San Lorenzello (Campania), XVIII secolo;
ceramica di Impruneta (Toscana).
Produzione di ceramica in Giappone |
Raku. Il termine giapponese Raku significa letteralmente comodo, rilassato, piacevole, gioia di vivere, deriva dal sobborgo di Kyōto da cui veniva estratta l'argilla nel sedicesimo secolo. Questa tecnica nasce in sintonia con lo spirito zen che esalta l'armonia presente nelle piccole cose e la bellezza nella semplicità e naturalezza delle forme. L'origine del Raku è legata alla cerimonia del tè: un rito, realizzato con oggetti poveri tra i quali il più importante era la tazza, che gli ospiti si scambiavano l'un l'altro. Le sue dimensioni erano tali da poter essere contenuta nel palmo della mano.- Porcellana di Imari
- Porcellana Kakiemon
Note |
^ ab Terracotta, in Treccani.it – Enciclopedie on line, Istituto dell'Enciclopedia Italiana, 15 marzo 2011. URL consultato il 22 aprile 2013.
^ terracòtta, in Sapere.it, De Agostini, 2012. URL consultato il 22 aprile 2013.
^ Cavalli-Sforza Geni, popoli e lingue, Milano, Adelphi, 1996. ISBN 88-459-1200-0
^ Vedere Li Liu, per maggiore precisione, in La révolution néolithique dans le monde, sotto la direzione di Jean-Paul Demoule, Inrap, 2009, p. 67, ISBN 978-2-271-06914-6.
^ Alain Testart, Avant l'histoire : L'évolution des sociétés de Lascaux à Carnac, NRF-Gallimard 2012, p. 38, nota 1, ISBN 978-2-07-013184-6.
^ Jean Guilaine, Caïn, Abel, Ötzi: L'héritage néolithique, Gallimard, 2011, p. 149, ISBN 978-2-07-013238-6.
^ Marcello Rotili e Nicola Busino, Castello di Ariano Irpino. Ricerche Archeologiche 1988-94, 2008 (PDF), in Quaderni di archeologia medievale, nº 11, Palermo, Officina di Studi Medievali, 2010, pp. 139-166, ISBN 978-88-6485-008-5.
^ M. Palvarini Gobio Casali, D. Ferrari (a cura di), Una credenza istoriata per Isabella d'Este, Mantova, Universitas Studiorum, 2014.
^ Universo, De Agostini, Novara, 1964, Vol. III, pag. 268-273
^ Antonello Maggipinto, Educare con la ceramica - Tecniche, esperienze e spunti operativi, ediz Junior, 2001. ISBN 88-86858-98-1
^ Distretti produttivi della ceramica, su laceramicaitaliana.it. URL consultato il settembre 2015.
^ Decreto del Ministro dell'industria, del commercio e dell'artigianato del 26 giugno 1997 in attuazione della Legge 9 luglio 1990
Bibliografia |
- Cipriano Piccolpasso, I tre libri dell'arte del vasajo : nei quali si tratta non solo la pratica, ma brevemente tutti i secreti di essa cosa che persino al di d'oggi e stata sempre tenuta nascosta,del cav. Cipriano Piccolpassi Durantino, Roma, dallo Stabilimento tipografico, 1857.
- T. Emiliani, E. Emiliani, Tecnologia dei Processi Ceramici, Società Editrice Ceramurgia s.r.l., Faenza, novembre 1982
- Daniela Di Castro e Roberto Valeriani, Il valore delle porcellane europee, Umberto Allemandi Editore, 1985
Enciclopedia Italiana Grolier, Grolier Hachette International, 1994
La porcellana di Venezia nel '700, Marsilio Editore, 1998- G.P. Emiliani, F. Corbara, Tecnologia Ceramica “Le Materie Prime”, vol.1, Faenza, Gruppo Editoriale Faenza Editrice S.p.A., gennaio 1999
- G.P. Emiliani, F.Corbara, Tecnologia Ceramica “Le Lavorazioni”, vol.2, Faenza, Gruppo Editoriale Faenza Editrice S.p.A., settembre 1999
- G.P. Emiliani, F. Corbara, Tecnologia Ceramica “Le Tipologie”, vol.3, Faenza, Gruppo Editoriale Faenza Editrice S.p.A., aprile 2001
- Maggipinto Antonello et al, Educare con la ceramica. Tecniche, esperienze e spunti operativi, Ediz. Junior, 2001, su edizionijunior.com.
Amedeo Benedetti, "Vetro, terracotta e ceramica", in Bibliografia Artigianato. La manualistica artigiana del Novecento: pubblicazioni su arti e mestieri in Italia dall'Unità ad oggi, Genova, Erga, 2004, pp. 350–367. ISBN 88-8163-358-2
- Andrea Ciaroni, Maioliche del Quattrocento a Pesaro. Frammenti di Storia dell'arte ceramica dalla bottega dei Fedeli, Firenze, edizioni Centro Di, 2004. ISBN 88-7038-404-7 Maioliche del Quattrocento a Pesaro: frammenti di storia dell'arte ceramica... - Andrea Ciaroni - Google Libri
La ceramica in Italia quando l'Italia non c'era, Edipuglia 2006
Le classi ceramiche. situazione degli studi. Atti della 10ª Giornata di Archeometria della Ceramica, Edipuglia 2009- Mariarosa Palvarini Gobio Casali e Daniela Ferrari (a cura di), Una "credenza" istoriata per Isabella d'Este. Il servizio di Nicola d'Urbino (...), Mantova, Universitas Studiorum, 2014, ISBN 978-88-97683-74-2.
- R. Viganò, Per uso della sua professione di lavorar faenze. Storia delle manifatture tra la seconda metà del XVI e gli inizi del XIX secolo, Monteroni di Lecce, 2013. ISBN 978-88-97895-10-7
- R. Viganò., “Bianco neretino. Un Prodotto di Donato Antonio Bonsegna sulla tavola degli osservanti di Nardò”, in «Spicilegia Sallentina. Rivista del caffè letterario di Nardò», n. 11 (2016), pp. 17-22.
- R. Viganò, Alla Mensa degli Angeli. Storia di ceramiche botteghe e vasai a Nardò tra i secoli XVI e XIX secolo, Monteroni di Lecce 2016. ISBN 978-88-97895 - 90-9
Voci correlate |
- Argilla
- Avventurina (vetro)
- Bellarmine
- Cavillatura
- Ceramica greca
- Ceramica almagra
- Maiolica
- Materiale ceramico
- Nero fratta
- Paper clay
- Pietra lavica ceramizzata
- Terracotta invetriata
- Terzo fuoco
Altri progetti |
Altri progetti
- Wikizionario
- Wikimedia Commons
Wikizionario contiene il lemma di dizionario «ceramica»
Wikimedia Commons contiene immagini o altri file su ceramica
Collegamenti esterni |
Ceramica, su Dizionario storico della Svizzera, hls-dhs-dss.ch.
Ceramica, su Treccani.it, Istituto dell'Enciclopedia Italiana.
Ceramica, su thes.bncf.firenze.sbn.it, Biblioteca Nazionale Centrale di Firenze.
http://www.archivioceramica.com Archivio della Ceramica Italiana del '900- La prima ceramica della storia? 20.000 anni fa, su lescienze.it.
.mw-parser-output .CdA{border:1px solid #aaa;width:100%;margin:auto;font-size:90%;padding:2px}.mw-parser-output .CdA th{background-color:#ddddff;font-weight:bold;width:20%}
Controllo di autorità | GND (DE) 4030270-2 · BNF (FR) cb11935435f (data) |
---|
v4 PoJ7V87cCpqwlwwyDb2sBno0L1,e,FlbjnarzZau1jZRXbn