Should I solder stranded wires when connecting them to a plug?
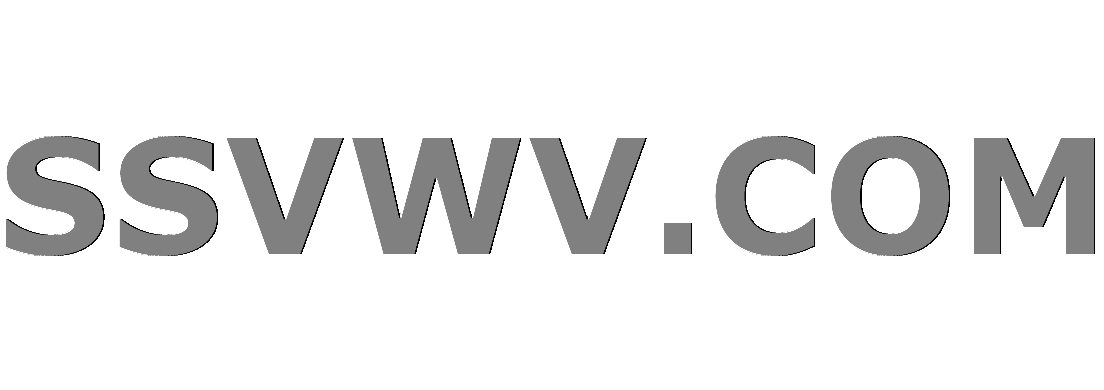
Multi tool use
I'm about to perform a few electrical changes in my house in order to be able to control lighting fixtures (230V, 30 to 200 mA) from a PC. I have some doubts about the way stranded wires should be connected to the plugs.
For instance, I suppose the way of connecting the wires shown on the next photo is dangerous, because the connection can easily become loose, is it? It seems that pulling the plug a few times by the wire instead of the plug itself would have disastrous effects on the connection.
If yes, should I solder stranded wire to make it solid? If so, what should I take care of, aside using a rosin-core solder? Once I solder it, how am I supposed to connect it to the metallic parts of the plug?
electrical wiring soldering
New contributor
Arseni Mourzenko is a new contributor to this site. Take care in asking for clarification, commenting, and answering.
Check out our Code of Conduct.
|
show 2 more comments
I'm about to perform a few electrical changes in my house in order to be able to control lighting fixtures (230V, 30 to 200 mA) from a PC. I have some doubts about the way stranded wires should be connected to the plugs.
For instance, I suppose the way of connecting the wires shown on the next photo is dangerous, because the connection can easily become loose, is it? It seems that pulling the plug a few times by the wire instead of the plug itself would have disastrous effects on the connection.
If yes, should I solder stranded wire to make it solid? If so, what should I take care of, aside using a rosin-core solder? Once I solder it, how am I supposed to connect it to the metallic parts of the plug?
electrical wiring soldering
New contributor
Arseni Mourzenko is a new contributor to this site. Take care in asking for clarification, commenting, and answering.
Check out our Code of Conduct.
15
The main concern I would have with that plug is the installation of the cord grip. the grip should be gripping on the sheath not the individual wires and it may need to be inverted for a good grip on a thin cable.
– Peter Green
Dec 24 at 21:47
1
I'd like to see it wrapped around the screw a little more; the ends wrapped around the tines do nothing.
– Mazura
Dec 25 at 19:08
4
Thank you for including the picture. This is NOT how it is supposed to be assembled. The screw terminal is supposed to hold the wire under compression and make a good electrical connection. You are not supposed to wrap the wire around the tines like that. Strain relief should be incorporated at the point where the cord enters the plug, so that even if you pull by the cord, no force is transferred to the screw wire joint.
– mkeith
Dec 26 at 4:03
@Mazura I don't think the wire is wrapped around the screw at all, it looks like the wire just sits next to the screw.
– Dan C
Dec 26 at 23:28
1
@jpmc26: thanks, changed. It may be common from persons speaking French because in French, one uses “I have a doubt” or “I have doubts” interchangeably in this context. Maybe things are similar in other languages as well.
– Arseni Mourzenko
2 days ago
|
show 2 more comments
I'm about to perform a few electrical changes in my house in order to be able to control lighting fixtures (230V, 30 to 200 mA) from a PC. I have some doubts about the way stranded wires should be connected to the plugs.
For instance, I suppose the way of connecting the wires shown on the next photo is dangerous, because the connection can easily become loose, is it? It seems that pulling the plug a few times by the wire instead of the plug itself would have disastrous effects on the connection.
If yes, should I solder stranded wire to make it solid? If so, what should I take care of, aside using a rosin-core solder? Once I solder it, how am I supposed to connect it to the metallic parts of the plug?
electrical wiring soldering
New contributor
Arseni Mourzenko is a new contributor to this site. Take care in asking for clarification, commenting, and answering.
Check out our Code of Conduct.
I'm about to perform a few electrical changes in my house in order to be able to control lighting fixtures (230V, 30 to 200 mA) from a PC. I have some doubts about the way stranded wires should be connected to the plugs.
For instance, I suppose the way of connecting the wires shown on the next photo is dangerous, because the connection can easily become loose, is it? It seems that pulling the plug a few times by the wire instead of the plug itself would have disastrous effects on the connection.
If yes, should I solder stranded wire to make it solid? If so, what should I take care of, aside using a rosin-core solder? Once I solder it, how am I supposed to connect it to the metallic parts of the plug?
electrical wiring soldering
electrical wiring soldering
New contributor
Arseni Mourzenko is a new contributor to this site. Take care in asking for clarification, commenting, and answering.
Check out our Code of Conduct.
New contributor
Arseni Mourzenko is a new contributor to this site. Take care in asking for clarification, commenting, and answering.
Check out our Code of Conduct.
edited 2 days ago
New contributor
Arseni Mourzenko is a new contributor to this site. Take care in asking for clarification, commenting, and answering.
Check out our Code of Conduct.
asked Dec 24 at 21:33
Arseni Mourzenko
16817
16817
New contributor
Arseni Mourzenko is a new contributor to this site. Take care in asking for clarification, commenting, and answering.
Check out our Code of Conduct.
New contributor
Arseni Mourzenko is a new contributor to this site. Take care in asking for clarification, commenting, and answering.
Check out our Code of Conduct.
Arseni Mourzenko is a new contributor to this site. Take care in asking for clarification, commenting, and answering.
Check out our Code of Conduct.
15
The main concern I would have with that plug is the installation of the cord grip. the grip should be gripping on the sheath not the individual wires and it may need to be inverted for a good grip on a thin cable.
– Peter Green
Dec 24 at 21:47
1
I'd like to see it wrapped around the screw a little more; the ends wrapped around the tines do nothing.
– Mazura
Dec 25 at 19:08
4
Thank you for including the picture. This is NOT how it is supposed to be assembled. The screw terminal is supposed to hold the wire under compression and make a good electrical connection. You are not supposed to wrap the wire around the tines like that. Strain relief should be incorporated at the point where the cord enters the plug, so that even if you pull by the cord, no force is transferred to the screw wire joint.
– mkeith
Dec 26 at 4:03
@Mazura I don't think the wire is wrapped around the screw at all, it looks like the wire just sits next to the screw.
– Dan C
Dec 26 at 23:28
1
@jpmc26: thanks, changed. It may be common from persons speaking French because in French, one uses “I have a doubt” or “I have doubts” interchangeably in this context. Maybe things are similar in other languages as well.
– Arseni Mourzenko
2 days ago
|
show 2 more comments
15
The main concern I would have with that plug is the installation of the cord grip. the grip should be gripping on the sheath not the individual wires and it may need to be inverted for a good grip on a thin cable.
– Peter Green
Dec 24 at 21:47
1
I'd like to see it wrapped around the screw a little more; the ends wrapped around the tines do nothing.
– Mazura
Dec 25 at 19:08
4
Thank you for including the picture. This is NOT how it is supposed to be assembled. The screw terminal is supposed to hold the wire under compression and make a good electrical connection. You are not supposed to wrap the wire around the tines like that. Strain relief should be incorporated at the point where the cord enters the plug, so that even if you pull by the cord, no force is transferred to the screw wire joint.
– mkeith
Dec 26 at 4:03
@Mazura I don't think the wire is wrapped around the screw at all, it looks like the wire just sits next to the screw.
– Dan C
Dec 26 at 23:28
1
@jpmc26: thanks, changed. It may be common from persons speaking French because in French, one uses “I have a doubt” or “I have doubts” interchangeably in this context. Maybe things are similar in other languages as well.
– Arseni Mourzenko
2 days ago
15
15
The main concern I would have with that plug is the installation of the cord grip. the grip should be gripping on the sheath not the individual wires and it may need to be inverted for a good grip on a thin cable.
– Peter Green
Dec 24 at 21:47
The main concern I would have with that plug is the installation of the cord grip. the grip should be gripping on the sheath not the individual wires and it may need to be inverted for a good grip on a thin cable.
– Peter Green
Dec 24 at 21:47
1
1
I'd like to see it wrapped around the screw a little more; the ends wrapped around the tines do nothing.
– Mazura
Dec 25 at 19:08
I'd like to see it wrapped around the screw a little more; the ends wrapped around the tines do nothing.
– Mazura
Dec 25 at 19:08
4
4
Thank you for including the picture. This is NOT how it is supposed to be assembled. The screw terminal is supposed to hold the wire under compression and make a good electrical connection. You are not supposed to wrap the wire around the tines like that. Strain relief should be incorporated at the point where the cord enters the plug, so that even if you pull by the cord, no force is transferred to the screw wire joint.
– mkeith
Dec 26 at 4:03
Thank you for including the picture. This is NOT how it is supposed to be assembled. The screw terminal is supposed to hold the wire under compression and make a good electrical connection. You are not supposed to wrap the wire around the tines like that. Strain relief should be incorporated at the point where the cord enters the plug, so that even if you pull by the cord, no force is transferred to the screw wire joint.
– mkeith
Dec 26 at 4:03
@Mazura I don't think the wire is wrapped around the screw at all, it looks like the wire just sits next to the screw.
– Dan C
Dec 26 at 23:28
@Mazura I don't think the wire is wrapped around the screw at all, it looks like the wire just sits next to the screw.
– Dan C
Dec 26 at 23:28
1
1
@jpmc26: thanks, changed. It may be common from persons speaking French because in French, one uses “I have a doubt” or “I have doubts” interchangeably in this context. Maybe things are similar in other languages as well.
– Arseni Mourzenko
2 days ago
@jpmc26: thanks, changed. It may be common from persons speaking French because in French, one uses “I have a doubt” or “I have doubts” interchangeably in this context. Maybe things are similar in other languages as well.
– Arseni Mourzenko
2 days ago
|
show 2 more comments
9 Answers
9
active
oldest
votes
It's a given that any wires in cordage will be stranded. Being designed for a different kind of service is what makes cordage different from in-wall wiring, and why you should not use one for the other.
So it's a given that any plug whose primary use is cordage is designed to work with stranded wire. Here, you should follow the instructions and labeling on the plugs, because following those instructions are the basis for the testing and certification which the plug received from your NRTL. (Nationally Recognized Testing Laboratory) such as UL, CSA, TUV etc.
Not following the instructions is an "off-label use" (to put it kindly) and can result in an illegal install and non-payout of fire insurance.
Speaking of non-payout, you need to be careful what you are sticking on mains power, and in particular, built into walls. Random electronic components out of the Digi-Key catalog are unfit for use in mains power. Equipment made for use in mains wiring can get its cert/listing faster if it is built with listed components, that is all a component listing means, it does not mean you can use components directly.
So for instance "random relay" is not listed for use in mains, but an "RIB" unit containing that same relay can be used. (RIB ~= Relay In Box).
If your aim is smart appliance control, you may be better off using existing, listed/certified smart devices (i.e. Not Sonoff), and having your electronics communicate with them. Generally, the rules are greatly relaxed for homebrew equipment when it is entirely low voltage and fed by a listed/certified wall wart.
1
+1 for saying wall wart, and even calling it certified :) I cannot believe how many people in my life have not understood that a wall wart is defined as a big ugly block known as cheap power adapter haha
– noybman
Dec 25 at 1:28
1
@noybman I assumed Harper meant certified as in "certified to be safe", rather than "certified to be a wart on the wall"?
– grawity
Dec 25 at 20:12
Indeed @grawity, I understood that. but they are certifiably ugly, and thus, the nickname. I don't know if you've ever seen the inside of a wall wart or a real transformer-regulator-filtered power supply, but the fact that labs actually certify wall warts is almost scary. They do their job, and are cheap. They just waste two slots in the process (usually)
– noybman
Dec 26 at 1:36
add a comment |
One should never apply lead alloy solder to stranded wires (often called "tinning") that are to be tightened under a screw. Eventually, the solder will cold-flow under the pressure and the screw connection will become loose.
This doesn't happen overnight; it can take months or years. I have personally seen this happen on several occasions.
It can be okay to just tin the very tip, to help keep the twisted wire strands together while tightening the screw. However, it is preferable just to leave some extra wire sticking out, and cut that off flush after tightening the screw.
New contributor
Mike Waters is a new contributor to this site. Take care in asking for clarification, commenting, and answering.
Check out our Code of Conduct.
1
Would this apply to stranded wire connected to a standard snap-in circuit breaker in an electrical panel? I believe I have read some recommendations on this site of using stranded wire for easier puling in conduit. So stranded wire would be connected to breakers, to gnd and neutral bars and to receptacles and switches. There was no mention of tinning AFIK.
– Jim Stewart
Dec 24 at 23:39
3
@JimStewart Yes. You're likely thinking of THHN wire. It should never be tinned, especially there.
– Mike Waters
Dec 25 at 2:01
I have never used THHN. For one thing I get uncomfortable whenever I have to strip wire with fine strands. I always cut some strands. How much strand cutting is acceptable? Is THHN specified for current capacity by AWG like solid wire? Why does NM cable use solid wire and not stranded?
– Jim Stewart
Dec 25 at 10:59
1
@JimStewart The CHSP is a special device and it uses that 50A breaker for a different purpose than breakers are typically used for. Their use of small gauge stranded wire is ok for that specific application. Stranded wire is fine to go into busbars - I like to just twist the ends tight before screwing them in. Tinning with solder is not a good idea for the reasons Mike stated but for the CHSP device, which draws no current unless correcting a transient, it's less dangerous and simply potentially limiting the device's full capability.
– J...
Dec 25 at 12:47
3
Code states solder only shall not be used and no solder on the ground , I build 480 3 phase 60-500 amp cords up and the power is soldered but the ground is clamped per NEC & mfg instructions. As for solid wire you will find it regularly in residential but not as often in commercial or industrial. A Nick in a solid wire is worse than cutting a couple fine strands because the nick becomes the breaking point for solid wire. Back stabs fail much more often but broken wires happen especially in high vibration locations this is why stranded wire is better plus it pulls easier.
– Ed Beal
Dec 25 at 15:12
|
show 2 more comments
With that style of terminal tinning the wires with solder is going to cause more problems than it solves.
However the plug in the picture does not look correctly wired to me.
Firstly the wires should wrap around the screws, not merely run down one side of them. They should be wrapped such that turning the screw will tighten the wire around the screw.
Secondly the cord grip does not seem to be correctly installed. It should clamp on the sheath not the individual conductors and it may need inverting to give a good grip on a thin cable or it may not be suitable for thin cables at all. If pulling the cord out puts stress on the electrical terminations the cord grip is not doing it's job properly.
add a comment |
I would not use solder - it won't help the grip much (arguably, stranded wire may actually grip the screw better as it deforms) and while it is probably not a bad conductor, it won't beat copper.
What is important is to wind the wire around the screws in the correct direction. To quote Harper from another answer (and I have seen him mention this quite a few times): Hook the wire clockwise around the screw, so tightening the screw makes it wrap more.
add a comment |
You should not use solder. The flat headed screw is designed to hold stranded wire in place. As other answers said, using solder will prevent the screw head getting a good grip on all the strands of wire and eventually it will work loose.
The mistake you made was to strip too much insulation from the wires and then try to make the joint stronger by wrapping the wire round the end of the pins after it went under the screw heads.
The correct way is to strip only enough insulation to make a loop around the screw, a bit LESS than one complete turn (about 3/4 of a turn is fine) so the wire doesn't overlap itself under the screw head. Wrap the wire round the screw in the direction so that tightening the screw pulls the wire tighter under the screw head rather than pushing it away.
The wires in your picture are coming towards the screw from the correct side, but they don't wrap far enough around the screw, because you thought you should wrap the end around the connector pins instead.
Exactly, and those screws are --or should be-- pan head screws. They have an undercut near the thread that helps hold the wire.
– Mike Waters
Dec 26 at 19:07
add a comment |
For the particular connection in the OP image, I would suggest using ring terminals on the wire, as they are intended to be screwed down:
I'm surprised that this excellent answer doesn't have more upvotes, as this is a superior method than using stranded wire under the screws. This photo shows insulated ring terminals. Where possible, they should be used in lieu of non-insulated crimp-type ring terminals. However, there is usually nothing wrong with the latter if there's not enough room for the former.
– Mike Waters
Dec 26 at 19:15
add a comment |
Generally speaking, no. The screws are designed to hold the wires in place.
If you don't feel the plug screws are sufficient, buy a newer one. They all use screws to connect, however.
add a comment |
- Use Electric wire ferrules:
"An electric wire ferrule (sometimes end terminal) is a metal tube
crimped over stranded wire to secure the strands within a screw
terminal."
The cord grip must clamp on the sheath of the whole cord and not just individual conductors.
Maybe most important: The earthing or grounding system is not connected! Either use a third conductor for earth/ground or use a plug which by design just has two conductors, if that is even permissible for the applied voltage and current.
New contributor
h.-m. muench is a new contributor to this site. Take care in asking for clarification, commenting, and answering.
Check out our Code of Conduct.
1
Ferrules are not suitable for use with that style of terminal, and it's perfectly normal to have a plug without the earth connected if the equipment downstream is class 2, what you don't want is a socket without the earth connected.
– Peter Green
Dec 26 at 2:59
I suppose one could take out the earth pin from the ICC plug, if there's only live and neutral wires to the appliance. But what's the point? If it's not connected to anything (double insulated doesn't need earth) there's no problem. Even if a wire comes loose and strays across to the earth pin (quite difficult but not impossible) the worst that will happen is no functioning of appliance, a blown fuse or trip.
– Tim
Dec 26 at 9:50
add a comment |
Soldering is fine, if it's a permanent installment. Reason being, what I often do is tin the stranded wire and solder it to the pin after removing the screw. That way, it's not ever going to come adrift. Obviously not the intended way, as screws are provided,but to my mind, it's a better electrical and probably physical connection. As also mentioned, the outer sheath needs to be under the clamp so that the people who insist on pulling the plug out by the wire don't put extra strain on the internals.
Please explain to a mere mortal why this isn't an acceptable thing to do. It's worked for me for 40 years so far!
– Tim
Dec 26 at 21:16
1
Potentially it can come adrift, especially if subjected to vibration. The "standard" way of doing it will have been determined by test labs in accelerated failure conditions.
– pjc50
2 days ago
@pjc50 - fair enough, except these plug/sockets aren't designed for use in vibration situations - they come apart by themselves then! Properly soldered, I've never had the wires come off in all that time. How long should they last..?
– Tim
2 days ago
add a comment |
Your Answer
StackExchange.ready(function() {
var channelOptions = {
tags: "".split(" "),
id: "73"
};
initTagRenderer("".split(" "), "".split(" "), channelOptions);
StackExchange.using("externalEditor", function() {
// Have to fire editor after snippets, if snippets enabled
if (StackExchange.settings.snippets.snippetsEnabled) {
StackExchange.using("snippets", function() {
createEditor();
});
}
else {
createEditor();
}
});
function createEditor() {
StackExchange.prepareEditor({
heartbeatType: 'answer',
autoActivateHeartbeat: false,
convertImagesToLinks: false,
noModals: true,
showLowRepImageUploadWarning: true,
reputationToPostImages: null,
bindNavPrevention: true,
postfix: "",
imageUploader: {
brandingHtml: "Powered by u003ca class="icon-imgur-white" href="https://imgur.com/"u003eu003c/au003e",
contentPolicyHtml: "User contributions licensed under u003ca href="https://creativecommons.org/licenses/by-sa/3.0/"u003ecc by-sa 3.0 with attribution requiredu003c/au003e u003ca href="https://stackoverflow.com/legal/content-policy"u003e(content policy)u003c/au003e",
allowUrls: true
},
noCode: true, onDemand: true,
discardSelector: ".discard-answer"
,immediatelyShowMarkdownHelp:true
});
}
});
Arseni Mourzenko is a new contributor. Be nice, and check out our Code of Conduct.
Sign up or log in
StackExchange.ready(function () {
StackExchange.helpers.onClickDraftSave('#login-link');
});
Sign up using Google
Sign up using Facebook
Sign up using Email and Password
Post as a guest
Required, but never shown
StackExchange.ready(
function () {
StackExchange.openid.initPostLogin('.new-post-login', 'https%3a%2f%2fdiy.stackexchange.com%2fquestions%2f153334%2fshould-i-solder-stranded-wires-when-connecting-them-to-a-plug%23new-answer', 'question_page');
}
);
Post as a guest
Required, but never shown
9 Answers
9
active
oldest
votes
9 Answers
9
active
oldest
votes
active
oldest
votes
active
oldest
votes
It's a given that any wires in cordage will be stranded. Being designed for a different kind of service is what makes cordage different from in-wall wiring, and why you should not use one for the other.
So it's a given that any plug whose primary use is cordage is designed to work with stranded wire. Here, you should follow the instructions and labeling on the plugs, because following those instructions are the basis for the testing and certification which the plug received from your NRTL. (Nationally Recognized Testing Laboratory) such as UL, CSA, TUV etc.
Not following the instructions is an "off-label use" (to put it kindly) and can result in an illegal install and non-payout of fire insurance.
Speaking of non-payout, you need to be careful what you are sticking on mains power, and in particular, built into walls. Random electronic components out of the Digi-Key catalog are unfit for use in mains power. Equipment made for use in mains wiring can get its cert/listing faster if it is built with listed components, that is all a component listing means, it does not mean you can use components directly.
So for instance "random relay" is not listed for use in mains, but an "RIB" unit containing that same relay can be used. (RIB ~= Relay In Box).
If your aim is smart appliance control, you may be better off using existing, listed/certified smart devices (i.e. Not Sonoff), and having your electronics communicate with them. Generally, the rules are greatly relaxed for homebrew equipment when it is entirely low voltage and fed by a listed/certified wall wart.
1
+1 for saying wall wart, and even calling it certified :) I cannot believe how many people in my life have not understood that a wall wart is defined as a big ugly block known as cheap power adapter haha
– noybman
Dec 25 at 1:28
1
@noybman I assumed Harper meant certified as in "certified to be safe", rather than "certified to be a wart on the wall"?
– grawity
Dec 25 at 20:12
Indeed @grawity, I understood that. but they are certifiably ugly, and thus, the nickname. I don't know if you've ever seen the inside of a wall wart or a real transformer-regulator-filtered power supply, but the fact that labs actually certify wall warts is almost scary. They do their job, and are cheap. They just waste two slots in the process (usually)
– noybman
Dec 26 at 1:36
add a comment |
It's a given that any wires in cordage will be stranded. Being designed for a different kind of service is what makes cordage different from in-wall wiring, and why you should not use one for the other.
So it's a given that any plug whose primary use is cordage is designed to work with stranded wire. Here, you should follow the instructions and labeling on the plugs, because following those instructions are the basis for the testing and certification which the plug received from your NRTL. (Nationally Recognized Testing Laboratory) such as UL, CSA, TUV etc.
Not following the instructions is an "off-label use" (to put it kindly) and can result in an illegal install and non-payout of fire insurance.
Speaking of non-payout, you need to be careful what you are sticking on mains power, and in particular, built into walls. Random electronic components out of the Digi-Key catalog are unfit for use in mains power. Equipment made for use in mains wiring can get its cert/listing faster if it is built with listed components, that is all a component listing means, it does not mean you can use components directly.
So for instance "random relay" is not listed for use in mains, but an "RIB" unit containing that same relay can be used. (RIB ~= Relay In Box).
If your aim is smart appliance control, you may be better off using existing, listed/certified smart devices (i.e. Not Sonoff), and having your electronics communicate with them. Generally, the rules are greatly relaxed for homebrew equipment when it is entirely low voltage and fed by a listed/certified wall wart.
1
+1 for saying wall wart, and even calling it certified :) I cannot believe how many people in my life have not understood that a wall wart is defined as a big ugly block known as cheap power adapter haha
– noybman
Dec 25 at 1:28
1
@noybman I assumed Harper meant certified as in "certified to be safe", rather than "certified to be a wart on the wall"?
– grawity
Dec 25 at 20:12
Indeed @grawity, I understood that. but they are certifiably ugly, and thus, the nickname. I don't know if you've ever seen the inside of a wall wart or a real transformer-regulator-filtered power supply, but the fact that labs actually certify wall warts is almost scary. They do their job, and are cheap. They just waste two slots in the process (usually)
– noybman
Dec 26 at 1:36
add a comment |
It's a given that any wires in cordage will be stranded. Being designed for a different kind of service is what makes cordage different from in-wall wiring, and why you should not use one for the other.
So it's a given that any plug whose primary use is cordage is designed to work with stranded wire. Here, you should follow the instructions and labeling on the plugs, because following those instructions are the basis for the testing and certification which the plug received from your NRTL. (Nationally Recognized Testing Laboratory) such as UL, CSA, TUV etc.
Not following the instructions is an "off-label use" (to put it kindly) and can result in an illegal install and non-payout of fire insurance.
Speaking of non-payout, you need to be careful what you are sticking on mains power, and in particular, built into walls. Random electronic components out of the Digi-Key catalog are unfit for use in mains power. Equipment made for use in mains wiring can get its cert/listing faster if it is built with listed components, that is all a component listing means, it does not mean you can use components directly.
So for instance "random relay" is not listed for use in mains, but an "RIB" unit containing that same relay can be used. (RIB ~= Relay In Box).
If your aim is smart appliance control, you may be better off using existing, listed/certified smart devices (i.e. Not Sonoff), and having your electronics communicate with them. Generally, the rules are greatly relaxed for homebrew equipment when it is entirely low voltage and fed by a listed/certified wall wart.
It's a given that any wires in cordage will be stranded. Being designed for a different kind of service is what makes cordage different from in-wall wiring, and why you should not use one for the other.
So it's a given that any plug whose primary use is cordage is designed to work with stranded wire. Here, you should follow the instructions and labeling on the plugs, because following those instructions are the basis for the testing and certification which the plug received from your NRTL. (Nationally Recognized Testing Laboratory) such as UL, CSA, TUV etc.
Not following the instructions is an "off-label use" (to put it kindly) and can result in an illegal install and non-payout of fire insurance.
Speaking of non-payout, you need to be careful what you are sticking on mains power, and in particular, built into walls. Random electronic components out of the Digi-Key catalog are unfit for use in mains power. Equipment made for use in mains wiring can get its cert/listing faster if it is built with listed components, that is all a component listing means, it does not mean you can use components directly.
So for instance "random relay" is not listed for use in mains, but an "RIB" unit containing that same relay can be used. (RIB ~= Relay In Box).
If your aim is smart appliance control, you may be better off using existing, listed/certified smart devices (i.e. Not Sonoff), and having your electronics communicate with them. Generally, the rules are greatly relaxed for homebrew equipment when it is entirely low voltage and fed by a listed/certified wall wart.
edited Dec 25 at 21:03
answered Dec 24 at 22:16
Harper
65.1k341133
65.1k341133
1
+1 for saying wall wart, and even calling it certified :) I cannot believe how many people in my life have not understood that a wall wart is defined as a big ugly block known as cheap power adapter haha
– noybman
Dec 25 at 1:28
1
@noybman I assumed Harper meant certified as in "certified to be safe", rather than "certified to be a wart on the wall"?
– grawity
Dec 25 at 20:12
Indeed @grawity, I understood that. but they are certifiably ugly, and thus, the nickname. I don't know if you've ever seen the inside of a wall wart or a real transformer-regulator-filtered power supply, but the fact that labs actually certify wall warts is almost scary. They do their job, and are cheap. They just waste two slots in the process (usually)
– noybman
Dec 26 at 1:36
add a comment |
1
+1 for saying wall wart, and even calling it certified :) I cannot believe how many people in my life have not understood that a wall wart is defined as a big ugly block known as cheap power adapter haha
– noybman
Dec 25 at 1:28
1
@noybman I assumed Harper meant certified as in "certified to be safe", rather than "certified to be a wart on the wall"?
– grawity
Dec 25 at 20:12
Indeed @grawity, I understood that. but they are certifiably ugly, and thus, the nickname. I don't know if you've ever seen the inside of a wall wart or a real transformer-regulator-filtered power supply, but the fact that labs actually certify wall warts is almost scary. They do their job, and are cheap. They just waste two slots in the process (usually)
– noybman
Dec 26 at 1:36
1
1
+1 for saying wall wart, and even calling it certified :) I cannot believe how many people in my life have not understood that a wall wart is defined as a big ugly block known as cheap power adapter haha
– noybman
Dec 25 at 1:28
+1 for saying wall wart, and even calling it certified :) I cannot believe how many people in my life have not understood that a wall wart is defined as a big ugly block known as cheap power adapter haha
– noybman
Dec 25 at 1:28
1
1
@noybman I assumed Harper meant certified as in "certified to be safe", rather than "certified to be a wart on the wall"?
– grawity
Dec 25 at 20:12
@noybman I assumed Harper meant certified as in "certified to be safe", rather than "certified to be a wart on the wall"?
– grawity
Dec 25 at 20:12
Indeed @grawity, I understood that. but they are certifiably ugly, and thus, the nickname. I don't know if you've ever seen the inside of a wall wart or a real transformer-regulator-filtered power supply, but the fact that labs actually certify wall warts is almost scary. They do their job, and are cheap. They just waste two slots in the process (usually)
– noybman
Dec 26 at 1:36
Indeed @grawity, I understood that. but they are certifiably ugly, and thus, the nickname. I don't know if you've ever seen the inside of a wall wart or a real transformer-regulator-filtered power supply, but the fact that labs actually certify wall warts is almost scary. They do their job, and are cheap. They just waste two slots in the process (usually)
– noybman
Dec 26 at 1:36
add a comment |
One should never apply lead alloy solder to stranded wires (often called "tinning") that are to be tightened under a screw. Eventually, the solder will cold-flow under the pressure and the screw connection will become loose.
This doesn't happen overnight; it can take months or years. I have personally seen this happen on several occasions.
It can be okay to just tin the very tip, to help keep the twisted wire strands together while tightening the screw. However, it is preferable just to leave some extra wire sticking out, and cut that off flush after tightening the screw.
New contributor
Mike Waters is a new contributor to this site. Take care in asking for clarification, commenting, and answering.
Check out our Code of Conduct.
1
Would this apply to stranded wire connected to a standard snap-in circuit breaker in an electrical panel? I believe I have read some recommendations on this site of using stranded wire for easier puling in conduit. So stranded wire would be connected to breakers, to gnd and neutral bars and to receptacles and switches. There was no mention of tinning AFIK.
– Jim Stewart
Dec 24 at 23:39
3
@JimStewart Yes. You're likely thinking of THHN wire. It should never be tinned, especially there.
– Mike Waters
Dec 25 at 2:01
I have never used THHN. For one thing I get uncomfortable whenever I have to strip wire with fine strands. I always cut some strands. How much strand cutting is acceptable? Is THHN specified for current capacity by AWG like solid wire? Why does NM cable use solid wire and not stranded?
– Jim Stewart
Dec 25 at 10:59
1
@JimStewart The CHSP is a special device and it uses that 50A breaker for a different purpose than breakers are typically used for. Their use of small gauge stranded wire is ok for that specific application. Stranded wire is fine to go into busbars - I like to just twist the ends tight before screwing them in. Tinning with solder is not a good idea for the reasons Mike stated but for the CHSP device, which draws no current unless correcting a transient, it's less dangerous and simply potentially limiting the device's full capability.
– J...
Dec 25 at 12:47
3
Code states solder only shall not be used and no solder on the ground , I build 480 3 phase 60-500 amp cords up and the power is soldered but the ground is clamped per NEC & mfg instructions. As for solid wire you will find it regularly in residential but not as often in commercial or industrial. A Nick in a solid wire is worse than cutting a couple fine strands because the nick becomes the breaking point for solid wire. Back stabs fail much more often but broken wires happen especially in high vibration locations this is why stranded wire is better plus it pulls easier.
– Ed Beal
Dec 25 at 15:12
|
show 2 more comments
One should never apply lead alloy solder to stranded wires (often called "tinning") that are to be tightened under a screw. Eventually, the solder will cold-flow under the pressure and the screw connection will become loose.
This doesn't happen overnight; it can take months or years. I have personally seen this happen on several occasions.
It can be okay to just tin the very tip, to help keep the twisted wire strands together while tightening the screw. However, it is preferable just to leave some extra wire sticking out, and cut that off flush after tightening the screw.
New contributor
Mike Waters is a new contributor to this site. Take care in asking for clarification, commenting, and answering.
Check out our Code of Conduct.
1
Would this apply to stranded wire connected to a standard snap-in circuit breaker in an electrical panel? I believe I have read some recommendations on this site of using stranded wire for easier puling in conduit. So stranded wire would be connected to breakers, to gnd and neutral bars and to receptacles and switches. There was no mention of tinning AFIK.
– Jim Stewart
Dec 24 at 23:39
3
@JimStewart Yes. You're likely thinking of THHN wire. It should never be tinned, especially there.
– Mike Waters
Dec 25 at 2:01
I have never used THHN. For one thing I get uncomfortable whenever I have to strip wire with fine strands. I always cut some strands. How much strand cutting is acceptable? Is THHN specified for current capacity by AWG like solid wire? Why does NM cable use solid wire and not stranded?
– Jim Stewart
Dec 25 at 10:59
1
@JimStewart The CHSP is a special device and it uses that 50A breaker for a different purpose than breakers are typically used for. Their use of small gauge stranded wire is ok for that specific application. Stranded wire is fine to go into busbars - I like to just twist the ends tight before screwing them in. Tinning with solder is not a good idea for the reasons Mike stated but for the CHSP device, which draws no current unless correcting a transient, it's less dangerous and simply potentially limiting the device's full capability.
– J...
Dec 25 at 12:47
3
Code states solder only shall not be used and no solder on the ground , I build 480 3 phase 60-500 amp cords up and the power is soldered but the ground is clamped per NEC & mfg instructions. As for solid wire you will find it regularly in residential but not as often in commercial or industrial. A Nick in a solid wire is worse than cutting a couple fine strands because the nick becomes the breaking point for solid wire. Back stabs fail much more often but broken wires happen especially in high vibration locations this is why stranded wire is better plus it pulls easier.
– Ed Beal
Dec 25 at 15:12
|
show 2 more comments
One should never apply lead alloy solder to stranded wires (often called "tinning") that are to be tightened under a screw. Eventually, the solder will cold-flow under the pressure and the screw connection will become loose.
This doesn't happen overnight; it can take months or years. I have personally seen this happen on several occasions.
It can be okay to just tin the very tip, to help keep the twisted wire strands together while tightening the screw. However, it is preferable just to leave some extra wire sticking out, and cut that off flush after tightening the screw.
New contributor
Mike Waters is a new contributor to this site. Take care in asking for clarification, commenting, and answering.
Check out our Code of Conduct.
One should never apply lead alloy solder to stranded wires (often called "tinning") that are to be tightened under a screw. Eventually, the solder will cold-flow under the pressure and the screw connection will become loose.
This doesn't happen overnight; it can take months or years. I have personally seen this happen on several occasions.
It can be okay to just tin the very tip, to help keep the twisted wire strands together while tightening the screw. However, it is preferable just to leave some extra wire sticking out, and cut that off flush after tightening the screw.
New contributor
Mike Waters is a new contributor to this site. Take care in asking for clarification, commenting, and answering.
Check out our Code of Conduct.
edited Dec 24 at 23:10
New contributor
Mike Waters is a new contributor to this site. Take care in asking for clarification, commenting, and answering.
Check out our Code of Conduct.
answered Dec 24 at 22:49


Mike Waters
37116
37116
New contributor
Mike Waters is a new contributor to this site. Take care in asking for clarification, commenting, and answering.
Check out our Code of Conduct.
New contributor
Mike Waters is a new contributor to this site. Take care in asking for clarification, commenting, and answering.
Check out our Code of Conduct.
Mike Waters is a new contributor to this site. Take care in asking for clarification, commenting, and answering.
Check out our Code of Conduct.
1
Would this apply to stranded wire connected to a standard snap-in circuit breaker in an electrical panel? I believe I have read some recommendations on this site of using stranded wire for easier puling in conduit. So stranded wire would be connected to breakers, to gnd and neutral bars and to receptacles and switches. There was no mention of tinning AFIK.
– Jim Stewart
Dec 24 at 23:39
3
@JimStewart Yes. You're likely thinking of THHN wire. It should never be tinned, especially there.
– Mike Waters
Dec 25 at 2:01
I have never used THHN. For one thing I get uncomfortable whenever I have to strip wire with fine strands. I always cut some strands. How much strand cutting is acceptable? Is THHN specified for current capacity by AWG like solid wire? Why does NM cable use solid wire and not stranded?
– Jim Stewart
Dec 25 at 10:59
1
@JimStewart The CHSP is a special device and it uses that 50A breaker for a different purpose than breakers are typically used for. Their use of small gauge stranded wire is ok for that specific application. Stranded wire is fine to go into busbars - I like to just twist the ends tight before screwing them in. Tinning with solder is not a good idea for the reasons Mike stated but for the CHSP device, which draws no current unless correcting a transient, it's less dangerous and simply potentially limiting the device's full capability.
– J...
Dec 25 at 12:47
3
Code states solder only shall not be used and no solder on the ground , I build 480 3 phase 60-500 amp cords up and the power is soldered but the ground is clamped per NEC & mfg instructions. As for solid wire you will find it regularly in residential but not as often in commercial or industrial. A Nick in a solid wire is worse than cutting a couple fine strands because the nick becomes the breaking point for solid wire. Back stabs fail much more often but broken wires happen especially in high vibration locations this is why stranded wire is better plus it pulls easier.
– Ed Beal
Dec 25 at 15:12
|
show 2 more comments
1
Would this apply to stranded wire connected to a standard snap-in circuit breaker in an electrical panel? I believe I have read some recommendations on this site of using stranded wire for easier puling in conduit. So stranded wire would be connected to breakers, to gnd and neutral bars and to receptacles and switches. There was no mention of tinning AFIK.
– Jim Stewart
Dec 24 at 23:39
3
@JimStewart Yes. You're likely thinking of THHN wire. It should never be tinned, especially there.
– Mike Waters
Dec 25 at 2:01
I have never used THHN. For one thing I get uncomfortable whenever I have to strip wire with fine strands. I always cut some strands. How much strand cutting is acceptable? Is THHN specified for current capacity by AWG like solid wire? Why does NM cable use solid wire and not stranded?
– Jim Stewart
Dec 25 at 10:59
1
@JimStewart The CHSP is a special device and it uses that 50A breaker for a different purpose than breakers are typically used for. Their use of small gauge stranded wire is ok for that specific application. Stranded wire is fine to go into busbars - I like to just twist the ends tight before screwing them in. Tinning with solder is not a good idea for the reasons Mike stated but for the CHSP device, which draws no current unless correcting a transient, it's less dangerous and simply potentially limiting the device's full capability.
– J...
Dec 25 at 12:47
3
Code states solder only shall not be used and no solder on the ground , I build 480 3 phase 60-500 amp cords up and the power is soldered but the ground is clamped per NEC & mfg instructions. As for solid wire you will find it regularly in residential but not as often in commercial or industrial. A Nick in a solid wire is worse than cutting a couple fine strands because the nick becomes the breaking point for solid wire. Back stabs fail much more often but broken wires happen especially in high vibration locations this is why stranded wire is better plus it pulls easier.
– Ed Beal
Dec 25 at 15:12
1
1
Would this apply to stranded wire connected to a standard snap-in circuit breaker in an electrical panel? I believe I have read some recommendations on this site of using stranded wire for easier puling in conduit. So stranded wire would be connected to breakers, to gnd and neutral bars and to receptacles and switches. There was no mention of tinning AFIK.
– Jim Stewart
Dec 24 at 23:39
Would this apply to stranded wire connected to a standard snap-in circuit breaker in an electrical panel? I believe I have read some recommendations on this site of using stranded wire for easier puling in conduit. So stranded wire would be connected to breakers, to gnd and neutral bars and to receptacles and switches. There was no mention of tinning AFIK.
– Jim Stewart
Dec 24 at 23:39
3
3
@JimStewart Yes. You're likely thinking of THHN wire. It should never be tinned, especially there.
– Mike Waters
Dec 25 at 2:01
@JimStewart Yes. You're likely thinking of THHN wire. It should never be tinned, especially there.
– Mike Waters
Dec 25 at 2:01
I have never used THHN. For one thing I get uncomfortable whenever I have to strip wire with fine strands. I always cut some strands. How much strand cutting is acceptable? Is THHN specified for current capacity by AWG like solid wire? Why does NM cable use solid wire and not stranded?
– Jim Stewart
Dec 25 at 10:59
I have never used THHN. For one thing I get uncomfortable whenever I have to strip wire with fine strands. I always cut some strands. How much strand cutting is acceptable? Is THHN specified for current capacity by AWG like solid wire? Why does NM cable use solid wire and not stranded?
– Jim Stewart
Dec 25 at 10:59
1
1
@JimStewart The CHSP is a special device and it uses that 50A breaker for a different purpose than breakers are typically used for. Their use of small gauge stranded wire is ok for that specific application. Stranded wire is fine to go into busbars - I like to just twist the ends tight before screwing them in. Tinning with solder is not a good idea for the reasons Mike stated but for the CHSP device, which draws no current unless correcting a transient, it's less dangerous and simply potentially limiting the device's full capability.
– J...
Dec 25 at 12:47
@JimStewart The CHSP is a special device and it uses that 50A breaker for a different purpose than breakers are typically used for. Their use of small gauge stranded wire is ok for that specific application. Stranded wire is fine to go into busbars - I like to just twist the ends tight before screwing them in. Tinning with solder is not a good idea for the reasons Mike stated but for the CHSP device, which draws no current unless correcting a transient, it's less dangerous and simply potentially limiting the device's full capability.
– J...
Dec 25 at 12:47
3
3
Code states solder only shall not be used and no solder on the ground , I build 480 3 phase 60-500 amp cords up and the power is soldered but the ground is clamped per NEC & mfg instructions. As for solid wire you will find it regularly in residential but not as often in commercial or industrial. A Nick in a solid wire is worse than cutting a couple fine strands because the nick becomes the breaking point for solid wire. Back stabs fail much more often but broken wires happen especially in high vibration locations this is why stranded wire is better plus it pulls easier.
– Ed Beal
Dec 25 at 15:12
Code states solder only shall not be used and no solder on the ground , I build 480 3 phase 60-500 amp cords up and the power is soldered but the ground is clamped per NEC & mfg instructions. As for solid wire you will find it regularly in residential but not as often in commercial or industrial. A Nick in a solid wire is worse than cutting a couple fine strands because the nick becomes the breaking point for solid wire. Back stabs fail much more often but broken wires happen especially in high vibration locations this is why stranded wire is better plus it pulls easier.
– Ed Beal
Dec 25 at 15:12
|
show 2 more comments
With that style of terminal tinning the wires with solder is going to cause more problems than it solves.
However the plug in the picture does not look correctly wired to me.
Firstly the wires should wrap around the screws, not merely run down one side of them. They should be wrapped such that turning the screw will tighten the wire around the screw.
Secondly the cord grip does not seem to be correctly installed. It should clamp on the sheath not the individual conductors and it may need inverting to give a good grip on a thin cable or it may not be suitable for thin cables at all. If pulling the cord out puts stress on the electrical terminations the cord grip is not doing it's job properly.
add a comment |
With that style of terminal tinning the wires with solder is going to cause more problems than it solves.
However the plug in the picture does not look correctly wired to me.
Firstly the wires should wrap around the screws, not merely run down one side of them. They should be wrapped such that turning the screw will tighten the wire around the screw.
Secondly the cord grip does not seem to be correctly installed. It should clamp on the sheath not the individual conductors and it may need inverting to give a good grip on a thin cable or it may not be suitable for thin cables at all. If pulling the cord out puts stress on the electrical terminations the cord grip is not doing it's job properly.
add a comment |
With that style of terminal tinning the wires with solder is going to cause more problems than it solves.
However the plug in the picture does not look correctly wired to me.
Firstly the wires should wrap around the screws, not merely run down one side of them. They should be wrapped such that turning the screw will tighten the wire around the screw.
Secondly the cord grip does not seem to be correctly installed. It should clamp on the sheath not the individual conductors and it may need inverting to give a good grip on a thin cable or it may not be suitable for thin cables at all. If pulling the cord out puts stress on the electrical terminations the cord grip is not doing it's job properly.
With that style of terminal tinning the wires with solder is going to cause more problems than it solves.
However the plug in the picture does not look correctly wired to me.
Firstly the wires should wrap around the screws, not merely run down one side of them. They should be wrapped such that turning the screw will tighten the wire around the screw.
Secondly the cord grip does not seem to be correctly installed. It should clamp on the sheath not the individual conductors and it may need inverting to give a good grip on a thin cable or it may not be suitable for thin cables at all. If pulling the cord out puts stress on the electrical terminations the cord grip is not doing it's job properly.
edited Dec 26 at 2:57
answered Dec 25 at 4:05
Peter Green
1,903514
1,903514
add a comment |
add a comment |
I would not use solder - it won't help the grip much (arguably, stranded wire may actually grip the screw better as it deforms) and while it is probably not a bad conductor, it won't beat copper.
What is important is to wind the wire around the screws in the correct direction. To quote Harper from another answer (and I have seen him mention this quite a few times): Hook the wire clockwise around the screw, so tightening the screw makes it wrap more.
add a comment |
I would not use solder - it won't help the grip much (arguably, stranded wire may actually grip the screw better as it deforms) and while it is probably not a bad conductor, it won't beat copper.
What is important is to wind the wire around the screws in the correct direction. To quote Harper from another answer (and I have seen him mention this quite a few times): Hook the wire clockwise around the screw, so tightening the screw makes it wrap more.
add a comment |
I would not use solder - it won't help the grip much (arguably, stranded wire may actually grip the screw better as it deforms) and while it is probably not a bad conductor, it won't beat copper.
What is important is to wind the wire around the screws in the correct direction. To quote Harper from another answer (and I have seen him mention this quite a few times): Hook the wire clockwise around the screw, so tightening the screw makes it wrap more.
I would not use solder - it won't help the grip much (arguably, stranded wire may actually grip the screw better as it deforms) and while it is probably not a bad conductor, it won't beat copper.
What is important is to wind the wire around the screws in the correct direction. To quote Harper from another answer (and I have seen him mention this quite a few times): Hook the wire clockwise around the screw, so tightening the screw makes it wrap more.
answered Dec 24 at 22:04
manassehkatz
6,7281029
6,7281029
add a comment |
add a comment |
You should not use solder. The flat headed screw is designed to hold stranded wire in place. As other answers said, using solder will prevent the screw head getting a good grip on all the strands of wire and eventually it will work loose.
The mistake you made was to strip too much insulation from the wires and then try to make the joint stronger by wrapping the wire round the end of the pins after it went under the screw heads.
The correct way is to strip only enough insulation to make a loop around the screw, a bit LESS than one complete turn (about 3/4 of a turn is fine) so the wire doesn't overlap itself under the screw head. Wrap the wire round the screw in the direction so that tightening the screw pulls the wire tighter under the screw head rather than pushing it away.
The wires in your picture are coming towards the screw from the correct side, but they don't wrap far enough around the screw, because you thought you should wrap the end around the connector pins instead.
Exactly, and those screws are --or should be-- pan head screws. They have an undercut near the thread that helps hold the wire.
– Mike Waters
Dec 26 at 19:07
add a comment |
You should not use solder. The flat headed screw is designed to hold stranded wire in place. As other answers said, using solder will prevent the screw head getting a good grip on all the strands of wire and eventually it will work loose.
The mistake you made was to strip too much insulation from the wires and then try to make the joint stronger by wrapping the wire round the end of the pins after it went under the screw heads.
The correct way is to strip only enough insulation to make a loop around the screw, a bit LESS than one complete turn (about 3/4 of a turn is fine) so the wire doesn't overlap itself under the screw head. Wrap the wire round the screw in the direction so that tightening the screw pulls the wire tighter under the screw head rather than pushing it away.
The wires in your picture are coming towards the screw from the correct side, but they don't wrap far enough around the screw, because you thought you should wrap the end around the connector pins instead.
Exactly, and those screws are --or should be-- pan head screws. They have an undercut near the thread that helps hold the wire.
– Mike Waters
Dec 26 at 19:07
add a comment |
You should not use solder. The flat headed screw is designed to hold stranded wire in place. As other answers said, using solder will prevent the screw head getting a good grip on all the strands of wire and eventually it will work loose.
The mistake you made was to strip too much insulation from the wires and then try to make the joint stronger by wrapping the wire round the end of the pins after it went under the screw heads.
The correct way is to strip only enough insulation to make a loop around the screw, a bit LESS than one complete turn (about 3/4 of a turn is fine) so the wire doesn't overlap itself under the screw head. Wrap the wire round the screw in the direction so that tightening the screw pulls the wire tighter under the screw head rather than pushing it away.
The wires in your picture are coming towards the screw from the correct side, but they don't wrap far enough around the screw, because you thought you should wrap the end around the connector pins instead.
You should not use solder. The flat headed screw is designed to hold stranded wire in place. As other answers said, using solder will prevent the screw head getting a good grip on all the strands of wire and eventually it will work loose.
The mistake you made was to strip too much insulation from the wires and then try to make the joint stronger by wrapping the wire round the end of the pins after it went under the screw heads.
The correct way is to strip only enough insulation to make a loop around the screw, a bit LESS than one complete turn (about 3/4 of a turn is fine) so the wire doesn't overlap itself under the screw head. Wrap the wire round the screw in the direction so that tightening the screw pulls the wire tighter under the screw head rather than pushing it away.
The wires in your picture are coming towards the screw from the correct side, but they don't wrap far enough around the screw, because you thought you should wrap the end around the connector pins instead.
answered Dec 25 at 10:27
alephzero
77647
77647
Exactly, and those screws are --or should be-- pan head screws. They have an undercut near the thread that helps hold the wire.
– Mike Waters
Dec 26 at 19:07
add a comment |
Exactly, and those screws are --or should be-- pan head screws. They have an undercut near the thread that helps hold the wire.
– Mike Waters
Dec 26 at 19:07
Exactly, and those screws are --or should be-- pan head screws. They have an undercut near the thread that helps hold the wire.
– Mike Waters
Dec 26 at 19:07
Exactly, and those screws are --or should be-- pan head screws. They have an undercut near the thread that helps hold the wire.
– Mike Waters
Dec 26 at 19:07
add a comment |
For the particular connection in the OP image, I would suggest using ring terminals on the wire, as they are intended to be screwed down:
I'm surprised that this excellent answer doesn't have more upvotes, as this is a superior method than using stranded wire under the screws. This photo shows insulated ring terminals. Where possible, they should be used in lieu of non-insulated crimp-type ring terminals. However, there is usually nothing wrong with the latter if there's not enough room for the former.
– Mike Waters
Dec 26 at 19:15
add a comment |
For the particular connection in the OP image, I would suggest using ring terminals on the wire, as they are intended to be screwed down:
I'm surprised that this excellent answer doesn't have more upvotes, as this is a superior method than using stranded wire under the screws. This photo shows insulated ring terminals. Where possible, they should be used in lieu of non-insulated crimp-type ring terminals. However, there is usually nothing wrong with the latter if there's not enough room for the former.
– Mike Waters
Dec 26 at 19:15
add a comment |
For the particular connection in the OP image, I would suggest using ring terminals on the wire, as they are intended to be screwed down:
For the particular connection in the OP image, I would suggest using ring terminals on the wire, as they are intended to be screwed down:
answered Dec 25 at 15:37
user2813274
1716
1716
I'm surprised that this excellent answer doesn't have more upvotes, as this is a superior method than using stranded wire under the screws. This photo shows insulated ring terminals. Where possible, they should be used in lieu of non-insulated crimp-type ring terminals. However, there is usually nothing wrong with the latter if there's not enough room for the former.
– Mike Waters
Dec 26 at 19:15
add a comment |
I'm surprised that this excellent answer doesn't have more upvotes, as this is a superior method than using stranded wire under the screws. This photo shows insulated ring terminals. Where possible, they should be used in lieu of non-insulated crimp-type ring terminals. However, there is usually nothing wrong with the latter if there's not enough room for the former.
– Mike Waters
Dec 26 at 19:15
I'm surprised that this excellent answer doesn't have more upvotes, as this is a superior method than using stranded wire under the screws. This photo shows insulated ring terminals. Where possible, they should be used in lieu of non-insulated crimp-type ring terminals. However, there is usually nothing wrong with the latter if there's not enough room for the former.
– Mike Waters
Dec 26 at 19:15
I'm surprised that this excellent answer doesn't have more upvotes, as this is a superior method than using stranded wire under the screws. This photo shows insulated ring terminals. Where possible, they should be used in lieu of non-insulated crimp-type ring terminals. However, there is usually nothing wrong with the latter if there's not enough room for the former.
– Mike Waters
Dec 26 at 19:15
add a comment |
Generally speaking, no. The screws are designed to hold the wires in place.
If you don't feel the plug screws are sufficient, buy a newer one. They all use screws to connect, however.
add a comment |
Generally speaking, no. The screws are designed to hold the wires in place.
If you don't feel the plug screws are sufficient, buy a newer one. They all use screws to connect, however.
add a comment |
Generally speaking, no. The screws are designed to hold the wires in place.
If you don't feel the plug screws are sufficient, buy a newer one. They all use screws to connect, however.
Generally speaking, no. The screws are designed to hold the wires in place.
If you don't feel the plug screws are sufficient, buy a newer one. They all use screws to connect, however.
answered Dec 24 at 21:42
Machavity
6,51511634
6,51511634
add a comment |
add a comment |
- Use Electric wire ferrules:
"An electric wire ferrule (sometimes end terminal) is a metal tube
crimped over stranded wire to secure the strands within a screw
terminal."
The cord grip must clamp on the sheath of the whole cord and not just individual conductors.
Maybe most important: The earthing or grounding system is not connected! Either use a third conductor for earth/ground or use a plug which by design just has two conductors, if that is even permissible for the applied voltage and current.
New contributor
h.-m. muench is a new contributor to this site. Take care in asking for clarification, commenting, and answering.
Check out our Code of Conduct.
1
Ferrules are not suitable for use with that style of terminal, and it's perfectly normal to have a plug without the earth connected if the equipment downstream is class 2, what you don't want is a socket without the earth connected.
– Peter Green
Dec 26 at 2:59
I suppose one could take out the earth pin from the ICC plug, if there's only live and neutral wires to the appliance. But what's the point? If it's not connected to anything (double insulated doesn't need earth) there's no problem. Even if a wire comes loose and strays across to the earth pin (quite difficult but not impossible) the worst that will happen is no functioning of appliance, a blown fuse or trip.
– Tim
Dec 26 at 9:50
add a comment |
- Use Electric wire ferrules:
"An electric wire ferrule (sometimes end terminal) is a metal tube
crimped over stranded wire to secure the strands within a screw
terminal."
The cord grip must clamp on the sheath of the whole cord and not just individual conductors.
Maybe most important: The earthing or grounding system is not connected! Either use a third conductor for earth/ground or use a plug which by design just has two conductors, if that is even permissible for the applied voltage and current.
New contributor
h.-m. muench is a new contributor to this site. Take care in asking for clarification, commenting, and answering.
Check out our Code of Conduct.
1
Ferrules are not suitable for use with that style of terminal, and it's perfectly normal to have a plug without the earth connected if the equipment downstream is class 2, what you don't want is a socket without the earth connected.
– Peter Green
Dec 26 at 2:59
I suppose one could take out the earth pin from the ICC plug, if there's only live and neutral wires to the appliance. But what's the point? If it's not connected to anything (double insulated doesn't need earth) there's no problem. Even if a wire comes loose and strays across to the earth pin (quite difficult but not impossible) the worst that will happen is no functioning of appliance, a blown fuse or trip.
– Tim
Dec 26 at 9:50
add a comment |
- Use Electric wire ferrules:
"An electric wire ferrule (sometimes end terminal) is a metal tube
crimped over stranded wire to secure the strands within a screw
terminal."
The cord grip must clamp on the sheath of the whole cord and not just individual conductors.
Maybe most important: The earthing or grounding system is not connected! Either use a third conductor for earth/ground or use a plug which by design just has two conductors, if that is even permissible for the applied voltage and current.
New contributor
h.-m. muench is a new contributor to this site. Take care in asking for clarification, commenting, and answering.
Check out our Code of Conduct.
- Use Electric wire ferrules:
"An electric wire ferrule (sometimes end terminal) is a metal tube
crimped over stranded wire to secure the strands within a screw
terminal."
The cord grip must clamp on the sheath of the whole cord and not just individual conductors.
Maybe most important: The earthing or grounding system is not connected! Either use a third conductor for earth/ground or use a plug which by design just has two conductors, if that is even permissible for the applied voltage and current.
New contributor
h.-m. muench is a new contributor to this site. Take care in asking for clarification, commenting, and answering.
Check out our Code of Conduct.
New contributor
h.-m. muench is a new contributor to this site. Take care in asking for clarification, commenting, and answering.
Check out our Code of Conduct.
answered Dec 25 at 18:48
h.-m. muench
11
11
New contributor
h.-m. muench is a new contributor to this site. Take care in asking for clarification, commenting, and answering.
Check out our Code of Conduct.
New contributor
h.-m. muench is a new contributor to this site. Take care in asking for clarification, commenting, and answering.
Check out our Code of Conduct.
h.-m. muench is a new contributor to this site. Take care in asking for clarification, commenting, and answering.
Check out our Code of Conduct.
1
Ferrules are not suitable for use with that style of terminal, and it's perfectly normal to have a plug without the earth connected if the equipment downstream is class 2, what you don't want is a socket without the earth connected.
– Peter Green
Dec 26 at 2:59
I suppose one could take out the earth pin from the ICC plug, if there's only live and neutral wires to the appliance. But what's the point? If it's not connected to anything (double insulated doesn't need earth) there's no problem. Even if a wire comes loose and strays across to the earth pin (quite difficult but not impossible) the worst that will happen is no functioning of appliance, a blown fuse or trip.
– Tim
Dec 26 at 9:50
add a comment |
1
Ferrules are not suitable for use with that style of terminal, and it's perfectly normal to have a plug without the earth connected if the equipment downstream is class 2, what you don't want is a socket without the earth connected.
– Peter Green
Dec 26 at 2:59
I suppose one could take out the earth pin from the ICC plug, if there's only live and neutral wires to the appliance. But what's the point? If it's not connected to anything (double insulated doesn't need earth) there's no problem. Even if a wire comes loose and strays across to the earth pin (quite difficult but not impossible) the worst that will happen is no functioning of appliance, a blown fuse or trip.
– Tim
Dec 26 at 9:50
1
1
Ferrules are not suitable for use with that style of terminal, and it's perfectly normal to have a plug without the earth connected if the equipment downstream is class 2, what you don't want is a socket without the earth connected.
– Peter Green
Dec 26 at 2:59
Ferrules are not suitable for use with that style of terminal, and it's perfectly normal to have a plug without the earth connected if the equipment downstream is class 2, what you don't want is a socket without the earth connected.
– Peter Green
Dec 26 at 2:59
I suppose one could take out the earth pin from the ICC plug, if there's only live and neutral wires to the appliance. But what's the point? If it's not connected to anything (double insulated doesn't need earth) there's no problem. Even if a wire comes loose and strays across to the earth pin (quite difficult but not impossible) the worst that will happen is no functioning of appliance, a blown fuse or trip.
– Tim
Dec 26 at 9:50
I suppose one could take out the earth pin from the ICC plug, if there's only live and neutral wires to the appliance. But what's the point? If it's not connected to anything (double insulated doesn't need earth) there's no problem. Even if a wire comes loose and strays across to the earth pin (quite difficult but not impossible) the worst that will happen is no functioning of appliance, a blown fuse or trip.
– Tim
Dec 26 at 9:50
add a comment |
Soldering is fine, if it's a permanent installment. Reason being, what I often do is tin the stranded wire and solder it to the pin after removing the screw. That way, it's not ever going to come adrift. Obviously not the intended way, as screws are provided,but to my mind, it's a better electrical and probably physical connection. As also mentioned, the outer sheath needs to be under the clamp so that the people who insist on pulling the plug out by the wire don't put extra strain on the internals.
Please explain to a mere mortal why this isn't an acceptable thing to do. It's worked for me for 40 years so far!
– Tim
Dec 26 at 21:16
1
Potentially it can come adrift, especially if subjected to vibration. The "standard" way of doing it will have been determined by test labs in accelerated failure conditions.
– pjc50
2 days ago
@pjc50 - fair enough, except these plug/sockets aren't designed for use in vibration situations - they come apart by themselves then! Properly soldered, I've never had the wires come off in all that time. How long should they last..?
– Tim
2 days ago
add a comment |
Soldering is fine, if it's a permanent installment. Reason being, what I often do is tin the stranded wire and solder it to the pin after removing the screw. That way, it's not ever going to come adrift. Obviously not the intended way, as screws are provided,but to my mind, it's a better electrical and probably physical connection. As also mentioned, the outer sheath needs to be under the clamp so that the people who insist on pulling the plug out by the wire don't put extra strain on the internals.
Please explain to a mere mortal why this isn't an acceptable thing to do. It's worked for me for 40 years so far!
– Tim
Dec 26 at 21:16
1
Potentially it can come adrift, especially if subjected to vibration. The "standard" way of doing it will have been determined by test labs in accelerated failure conditions.
– pjc50
2 days ago
@pjc50 - fair enough, except these plug/sockets aren't designed for use in vibration situations - they come apart by themselves then! Properly soldered, I've never had the wires come off in all that time. How long should they last..?
– Tim
2 days ago
add a comment |
Soldering is fine, if it's a permanent installment. Reason being, what I often do is tin the stranded wire and solder it to the pin after removing the screw. That way, it's not ever going to come adrift. Obviously not the intended way, as screws are provided,but to my mind, it's a better electrical and probably physical connection. As also mentioned, the outer sheath needs to be under the clamp so that the people who insist on pulling the plug out by the wire don't put extra strain on the internals.
Soldering is fine, if it's a permanent installment. Reason being, what I often do is tin the stranded wire and solder it to the pin after removing the screw. That way, it's not ever going to come adrift. Obviously not the intended way, as screws are provided,but to my mind, it's a better electrical and probably physical connection. As also mentioned, the outer sheath needs to be under the clamp so that the people who insist on pulling the plug out by the wire don't put extra strain on the internals.
answered Dec 26 at 9:43
Tim
22916
22916
Please explain to a mere mortal why this isn't an acceptable thing to do. It's worked for me for 40 years so far!
– Tim
Dec 26 at 21:16
1
Potentially it can come adrift, especially if subjected to vibration. The "standard" way of doing it will have been determined by test labs in accelerated failure conditions.
– pjc50
2 days ago
@pjc50 - fair enough, except these plug/sockets aren't designed for use in vibration situations - they come apart by themselves then! Properly soldered, I've never had the wires come off in all that time. How long should they last..?
– Tim
2 days ago
add a comment |
Please explain to a mere mortal why this isn't an acceptable thing to do. It's worked for me for 40 years so far!
– Tim
Dec 26 at 21:16
1
Potentially it can come adrift, especially if subjected to vibration. The "standard" way of doing it will have been determined by test labs in accelerated failure conditions.
– pjc50
2 days ago
@pjc50 - fair enough, except these plug/sockets aren't designed for use in vibration situations - they come apart by themselves then! Properly soldered, I've never had the wires come off in all that time. How long should they last..?
– Tim
2 days ago
Please explain to a mere mortal why this isn't an acceptable thing to do. It's worked for me for 40 years so far!
– Tim
Dec 26 at 21:16
Please explain to a mere mortal why this isn't an acceptable thing to do. It's worked for me for 40 years so far!
– Tim
Dec 26 at 21:16
1
1
Potentially it can come adrift, especially if subjected to vibration. The "standard" way of doing it will have been determined by test labs in accelerated failure conditions.
– pjc50
2 days ago
Potentially it can come adrift, especially if subjected to vibration. The "standard" way of doing it will have been determined by test labs in accelerated failure conditions.
– pjc50
2 days ago
@pjc50 - fair enough, except these plug/sockets aren't designed for use in vibration situations - they come apart by themselves then! Properly soldered, I've never had the wires come off in all that time. How long should they last..?
– Tim
2 days ago
@pjc50 - fair enough, except these plug/sockets aren't designed for use in vibration situations - they come apart by themselves then! Properly soldered, I've never had the wires come off in all that time. How long should they last..?
– Tim
2 days ago
add a comment |
Arseni Mourzenko is a new contributor. Be nice, and check out our Code of Conduct.
Arseni Mourzenko is a new contributor. Be nice, and check out our Code of Conduct.
Arseni Mourzenko is a new contributor. Be nice, and check out our Code of Conduct.
Arseni Mourzenko is a new contributor. Be nice, and check out our Code of Conduct.
Thanks for contributing an answer to Home Improvement Stack Exchange!
- Please be sure to answer the question. Provide details and share your research!
But avoid …
- Asking for help, clarification, or responding to other answers.
- Making statements based on opinion; back them up with references or personal experience.
To learn more, see our tips on writing great answers.
Some of your past answers have not been well-received, and you're in danger of being blocked from answering.
Please pay close attention to the following guidance:
- Please be sure to answer the question. Provide details and share your research!
But avoid …
- Asking for help, clarification, or responding to other answers.
- Making statements based on opinion; back them up with references or personal experience.
To learn more, see our tips on writing great answers.
Sign up or log in
StackExchange.ready(function () {
StackExchange.helpers.onClickDraftSave('#login-link');
});
Sign up using Google
Sign up using Facebook
Sign up using Email and Password
Post as a guest
Required, but never shown
StackExchange.ready(
function () {
StackExchange.openid.initPostLogin('.new-post-login', 'https%3a%2f%2fdiy.stackexchange.com%2fquestions%2f153334%2fshould-i-solder-stranded-wires-when-connecting-them-to-a-plug%23new-answer', 'question_page');
}
);
Post as a guest
Required, but never shown
Sign up or log in
StackExchange.ready(function () {
StackExchange.helpers.onClickDraftSave('#login-link');
});
Sign up using Google
Sign up using Facebook
Sign up using Email and Password
Post as a guest
Required, but never shown
Sign up or log in
StackExchange.ready(function () {
StackExchange.helpers.onClickDraftSave('#login-link');
});
Sign up using Google
Sign up using Facebook
Sign up using Email and Password
Post as a guest
Required, but never shown
Sign up or log in
StackExchange.ready(function () {
StackExchange.helpers.onClickDraftSave('#login-link');
});
Sign up using Google
Sign up using Facebook
Sign up using Email and Password
Sign up using Google
Sign up using Facebook
Sign up using Email and Password
Post as a guest
Required, but never shown
Required, but never shown
Required, but never shown
Required, but never shown
Required, but never shown
Required, but never shown
Required, but never shown
Required, but never shown
Required, but never shown
auDxiTiy4YupM0vvpCmsvGIRNi0J
15
The main concern I would have with that plug is the installation of the cord grip. the grip should be gripping on the sheath not the individual wires and it may need to be inverted for a good grip on a thin cable.
– Peter Green
Dec 24 at 21:47
1
I'd like to see it wrapped around the screw a little more; the ends wrapped around the tines do nothing.
– Mazura
Dec 25 at 19:08
4
Thank you for including the picture. This is NOT how it is supposed to be assembled. The screw terminal is supposed to hold the wire under compression and make a good electrical connection. You are not supposed to wrap the wire around the tines like that. Strain relief should be incorporated at the point where the cord enters the plug, so that even if you pull by the cord, no force is transferred to the screw wire joint.
– mkeith
Dec 26 at 4:03
@Mazura I don't think the wire is wrapped around the screw at all, it looks like the wire just sits next to the screw.
– Dan C
Dec 26 at 23:28
1
@jpmc26: thanks, changed. It may be common from persons speaking French because in French, one uses “I have a doubt” or “I have doubts” interchangeably in this context. Maybe things are similar in other languages as well.
– Arseni Mourzenko
2 days ago